Ponad 100 lat poświęconych postępowi technicznemu - tak najprościej można opisać naszą działalność w zakresie technologii robotycznej i automatyki Yaskawa.
Bomag stawia na zrobotyzowane szlifowanie spoin
MOTOMAN MH180 zapewnia perfekcyjną gładkość spoin
W zakładach produkcyjnych firmy Bomag aż roi się od nowoczesnych technologii. Wiele zadań przy produkcji bębnów walców do robót ziemnych wykonują tu roboty, a ostatnio jednostki robotyczne zatrudniono także do czyszczenia spoin. Efekt przerósł oczekiwania producenta: wielotonowy bęben zyskał idealnie okrągły kształt, a przyszła szosa – perfekcyjnie gładką nawierzchnię.
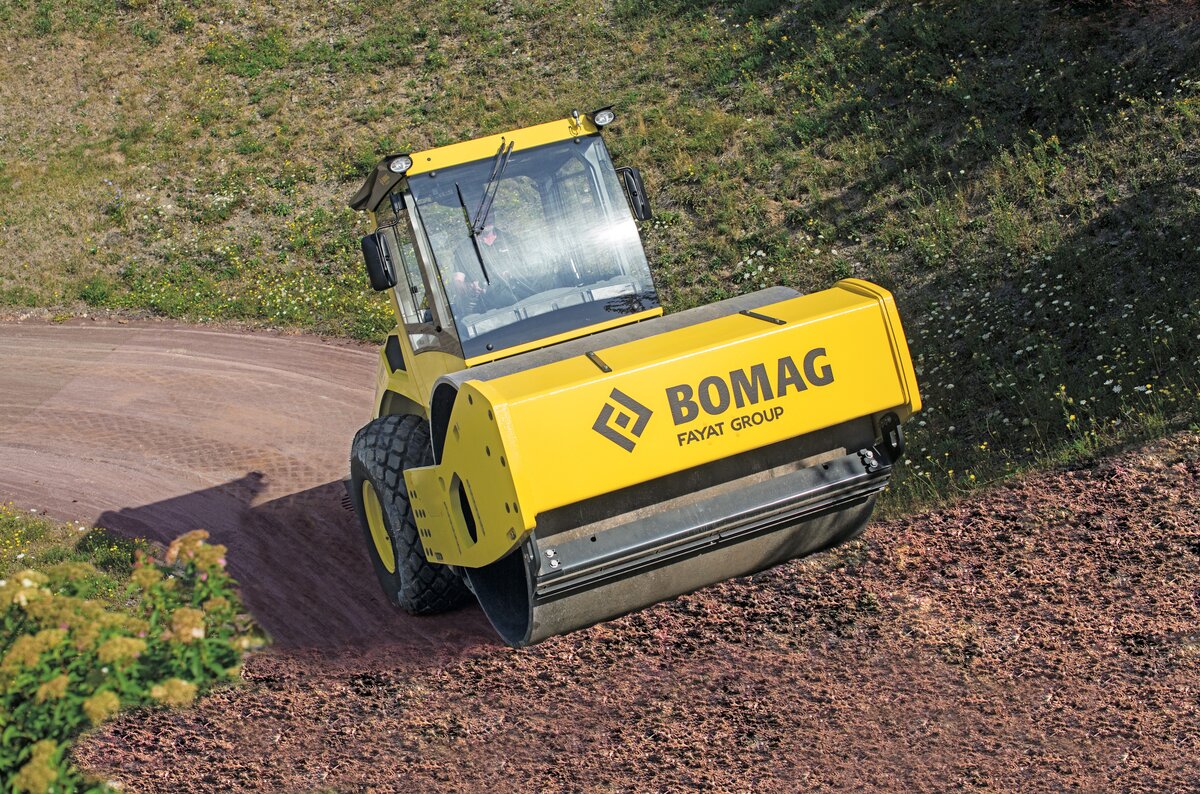
Produkowane przez Bomag bębny ważą niekiedy i 12 ton. Montowane w maszynach drogowych, służą do zagęszczania gruntu pod budowę dróg, m.in. dzięki funkcji generowania wibracji. Niemieckie przedsiębiorstwo z siedzibą w Boppard jest zdecydowanym liderem rynkowym na tym wymagającym polu, stale inwestując w nowe technologie produkcji.
W 2013 r. Bomag uruchomił nowy zakład produkcyjny specjalizujący się w wytwarzaniu bębnów walców do robót ziemnych. Bębny produkowane są z blachy okładzinowej o grubości do 60 mm, częściowo wykonanej z trudnościeralnej stali Hardox. Każda z nich jest najpierw wyoblana z siłą zginającą nawet 6000 ton, a następnie poddawana obróbce spawaniem. Proces ten realizowany jest całkowicie automatycznie, a jego celem jest wytworzenie trzech spoin: wzdłużnej oraz dwóch po okręgu (łączących koła tarczowe z korpusem wału). Ostatnim krokiem jest precyzyjne oczyszczenie spoin, w tym zwłaszcza spoiny wzdłużnej, której gładkość ma bezpośredni wpływ na jakość podbudowy, czyli warstwy poziomujące znajdującej się bezpośrednio pod nawierzchnią drogi.
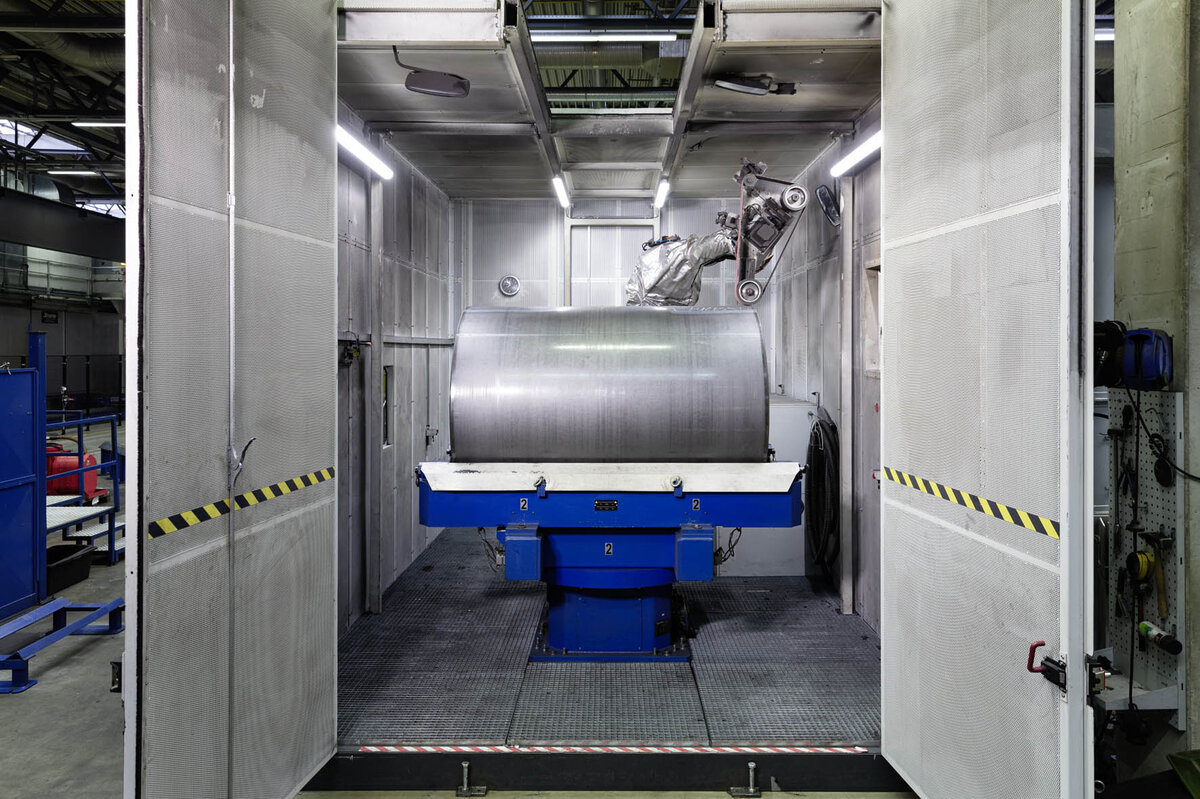
Alternatywa dla frezowania wzdłużnego
Początkowo w procesie tym wykorzystywano frezarkę wzdłużną. Maszyna, wykonując ruch liniowy, co prawda efektywnie obcinała naddatki spoiny, ale przy okazji generowała ogromny hałas i wzniecała tumany pyłu. Nie była też tak dokładna, jak oczekiwał Bomag.
Firma zaczęła więc poszukiwać alternatywnych rozwiązań, bacznie rozglądając się także po rynku robotyki. Już wcześniej sporo inwestowała bowiem w różnorodne środki automatyzacji, wykorzystując je nie tylko w szeregu procesów z zakresu obróbki bębnów, ale także do transportu materiału. Idealnie sprawdziły się tutaj wózki samojezdne AGV o dużym udźwigu.
Wykonawcę znalazła przypadkiem: Harald Aßmann, kierownik zakładu produkcji bębnów, odpowiedział na zaproszenie firmy Yaskawa i odwiedził ją w trakcie dni otwartych. Korzystając z okazji, wypytał producenta o możliwość wykorzystania robotów w procesie szlifowania. Odpowiedź całkowicie go usatysfakcjonowała. „Mogliśmy obejrzeć konkretne przykłady wdrożeń robotów szlifierskich. To przekonało nas, że Yaskawa jest dla nas odpowiednim partnerem”, mówi Harald Aßmann.
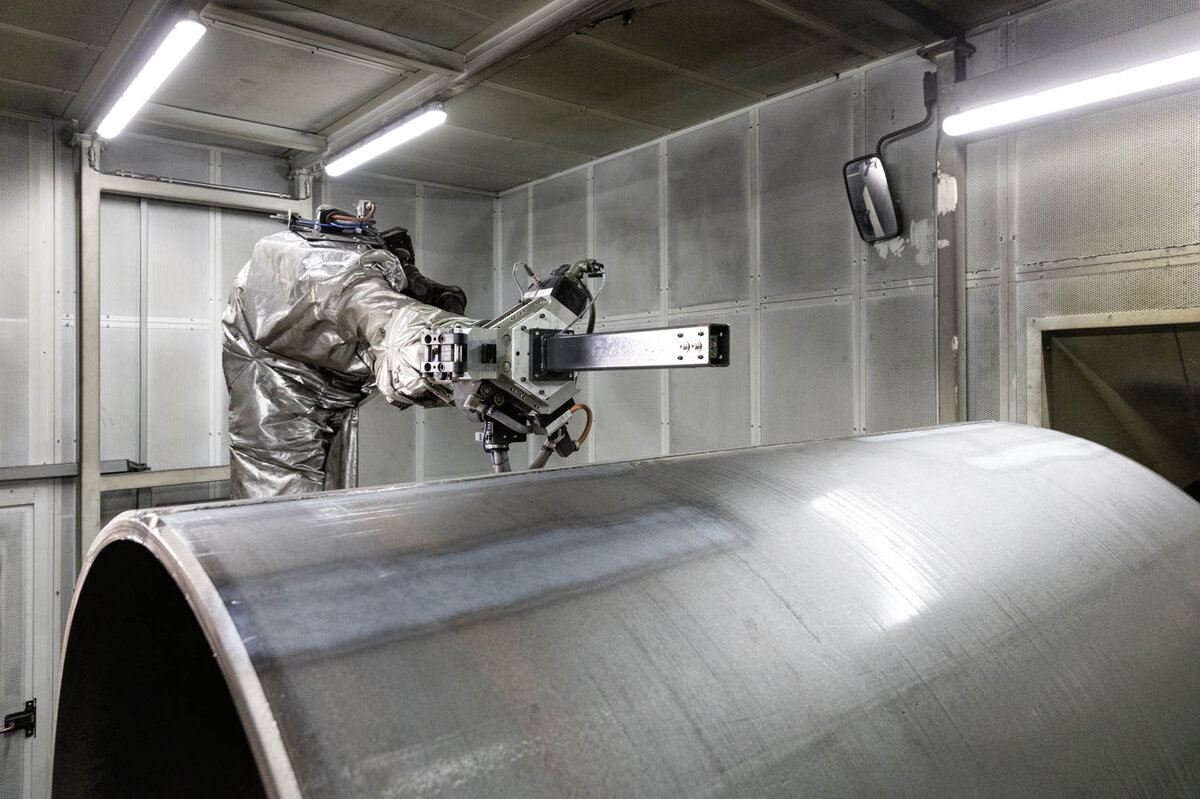
Krok 1: pomiar spoiny
Dzięki ścisłej współpracy z firmą Bomag Yaskawa w krótkim czasie opracowała i wdrożyła całkowicie zabudowany system do obróbki szlifierskiej składający się z robota, suwnicy wprowadzającej bęben do komory obróbczej oraz obrotowego pozycjonera bębna, który mocuje go tak, by spoina była skierowana pionowo w górę.
Po wprowadzeniu bębna do pozycjonera operator uruchamia program obróbczy i zamyka komorę. Teraz do akcji wkracza sześcioosiowy robot MOTOMAN MH180: jednostka pobiera miernik laserowy z magazynu narzędzi i rozpoczyna pomiar spoiny, poruszając się nie ruchem liniowym, lecz wahadłowym. Dzięki temu może dokładnie zmierzyć spoinę w trzech wymiarach.

Krok 2 i 3: szlifowanie spoiny wzdłużnej i kół tarczowych
Zebrane dane zostaną wykorzystane w kolejnej fazie obróbki. Aby się do niej przygotować, robot znów sięga do magazynu narzędziowego i wymienia miernik na szlifierkę taśmową, a następnie rozpoczyna szlifowanie spoiny. Aby uzyskać optymalny wynik tego procesu, potrzeba z reguły 10 do 12 przejść. Skąd system wie, że spoina ma właściwą jakość? Informuje go o tym ilość prądu zużywanego przez szlifierkę: jeśli narzędzie usunęło cały naddatek, kolejne przejazdy generują mniejszy opór, a tym samym wymagają dostarczenia mniejszej ilości energii. Dla robota jest to sygnał do zakończenia pracy i przejścia do kolejnego kroku, tj. szlifowania boków wału.
Także podczas szlifowania robot porusza się ruchem nieliniowym, dzięki czemu może dokładnie oczyścić całą powierzchnię spoiny. Pomaga mu w tym także ruch obrotowy pozycjoner. „Dzięki temu oszczędzamy sporo przestrzeni: robot ma co prawda ogromny zasięg, ale w przypadku dużych bębnów nie wystarcza on do oszlifowania spoiny na całej długości ich długości”, wyjaśnia Harald Aßmann.
Ruch obrotowy pozycjonera umożliwia także realizację trzeciego i ostatniego kroku obróbki, w którym robot – po wymianie szlifierki taśmowej na mimośrodową – czyści spoiny na połączeniu kół tarczowych z korpusem bębna. Efektem trójfazowego procesu jest idealnie gładka spoina wzdłużna, całkowicie wyrównana z powierzchnią wału oraz dokładnie oczyszczone spoiny kół tarczowych.
Co nietypowe, magazyn narzędziowy „robota czyszczącego”, bo tak nazywa go Bomag, jest zabezpieczony od góry klapą otwierającą się automatycznie jedynie w momencie wymiany narzędzi. Dzięki temu narzędzia są odpowiednio zabezpieczone przed pyłem. Podobną funkcję pełni osłona szczelnie otulająca korpus robota. Stanowi ona także dodatkowe zabezpieczenie przed iskrami – na wypadek, gdyby któraś z nich nie została wychwycona przez system odciągowy.
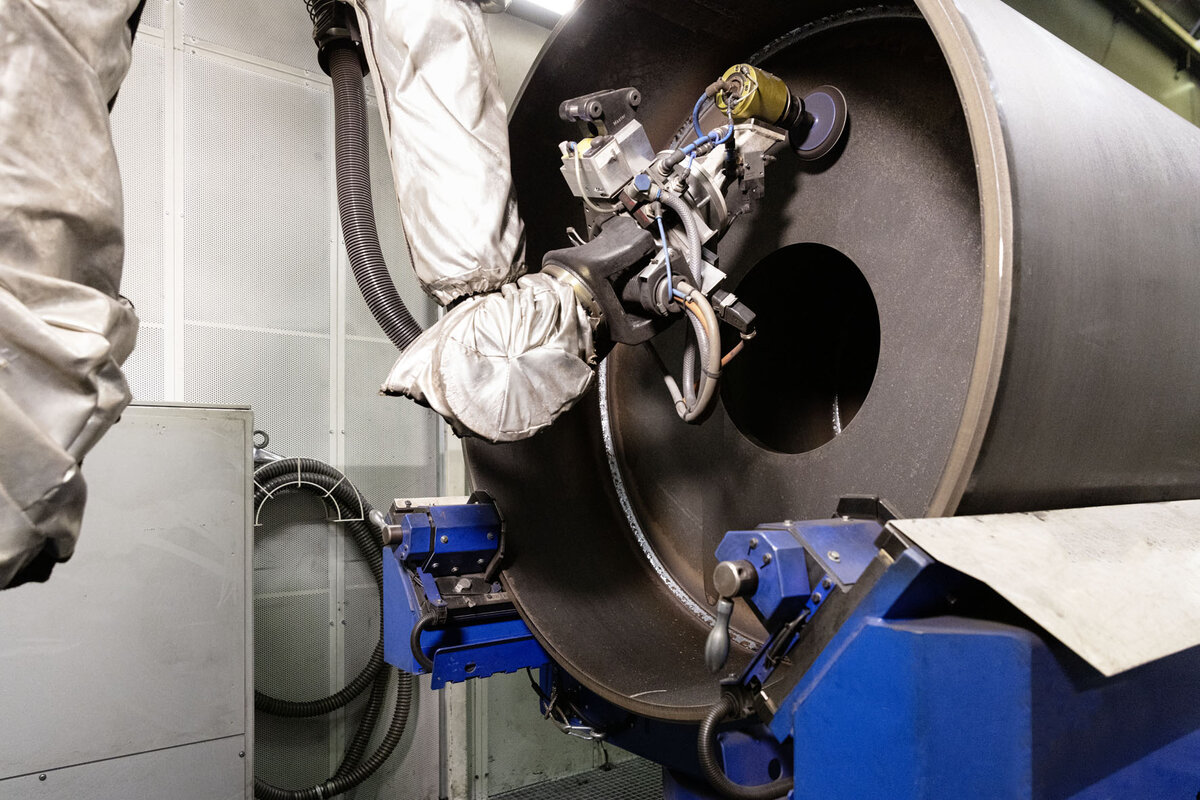
Dobrze wykorzystany czas
Z punktu widzenia produktywności ogromną zaletą systemu jest to, że czyszczenie realizowane jest równolegle z innymi pracami obróbczymi. „W czasie szlifowania jednocześnie nawiercane są otwory w kołach tarczowych”, mówi Harald Aßmann.
Dennis Anton, programista robota, chwali go również za dużą elastyczność, którą zdążył się już wykazać przez sześć pierwszych miesięcy pracy: „W tym czasie przygotowaliśmy programy obróbcze blisko 40 typów bębnów o najróżniejszych długościach i średnicach dochodzących do ponad 2 metrów”.
Przedsiębiorstwo pozytywnie ocenia również samą realizację projektu, w tym możliwość wprowadzania „niewielkich poprawek” na miejscu. Dennis Anton zaproponował na przykład, aby wykorzystać zintegrowaną z robotem instalację pneumatyczną do usuwania pozostałości odprysków spawalniczych i pyłu szlifierskiego z wnętrza bębna.
Firma Bomag bardzo pozytywnie ocenia projekt. „Nasza produktywność wzrosła, bo pracownicy nie muszą już manualnie doszlifowywać ani czyścić spoin. Dodatkowo mogą poświęcić się bardziej wymagającym zadaniom, bo proste, fizyczne czynności wykonuje za nich robot”, podsumowuje Harald Aßmann. A cały zakład wreszcie odetchnął z ulgą, gdyż system niemal nie generuje pyłu ani hałasu.
Tekst: Ralf Högel
Zdjęcia: Yaskawa