Ponad 100 lat poświęconych postępowi technicznemu - tak najprościej można opisać naszą działalność w zakresie technologii robotycznej i automatyki Yaskawa.
Maski "made in Germany"
Elastyczna technika automatyzacji dla produkcji maszynowej specjalnego przeznaczenia
Wraz z nadejściem pandemii koronawirusa gwałtownie wzrosło zapotrzebowanie na maski ochronne FFP2. W początkowym okresie brakowało jednak mocy produkcyjnych. W roku 2020 szybko się to zmieniło. Doświadczeni inżynierowie zareagowali błyskawicznie i byli w stanie zaoferować wydajne rozwiązania "made in Germany" w zadziwiająco krótkim czasie. Jednym z dostawców, który bardzo szybko wdrożył koncepcję maszyny we współpracy ze specjalistą w dziedzinie automatyzacji, firmą Yaskawa, był producent maszyn specjalnych Unimatic Automationssysteme GmbH z Grub am Forst niedaleko Coburga. Koncepcja ta powstała w wyniku zastosowania wydajnej technologii napędów i sterowania firmy Yaskawa i efektywnej współpracy obu partnerów.
Kiedy w marcu 2020 roku rząd stwierdził, że brakuje sprzętu ochrony medycznej, zlecił jego produkcję niemieckim firmom. Jednak większość z nich nie posiadała odpowiedniego zaplecza. Firma Unimatic Automationssysteme GmbH otrzymała od klienta zapytanie o możliwość zbudowania w krótkim czasie systemu produkcyjnego dla masek ochronnych FFP2. Producent maszyn specjalnych nie zawahał się podjąć tego wyzwania. Firma zwróciła się do kolegów z Unimatic China, którzy mieli już cenne doświadczenie w tej dziedzinie. "W ramach wspólnego przedsięwzięcia z Chinami opracowaliśmy koncepcję systemu i dostosowaliśmy ją do standardów rynku europejskiego", relacjonuje dr Robert Kahlau, szef działu robotyki w Unimatic. "Klient początkowo zlecił wykonanie czterech systemów, ale ostateczne zamówiono łącznie osiem linii produkcyjnych".
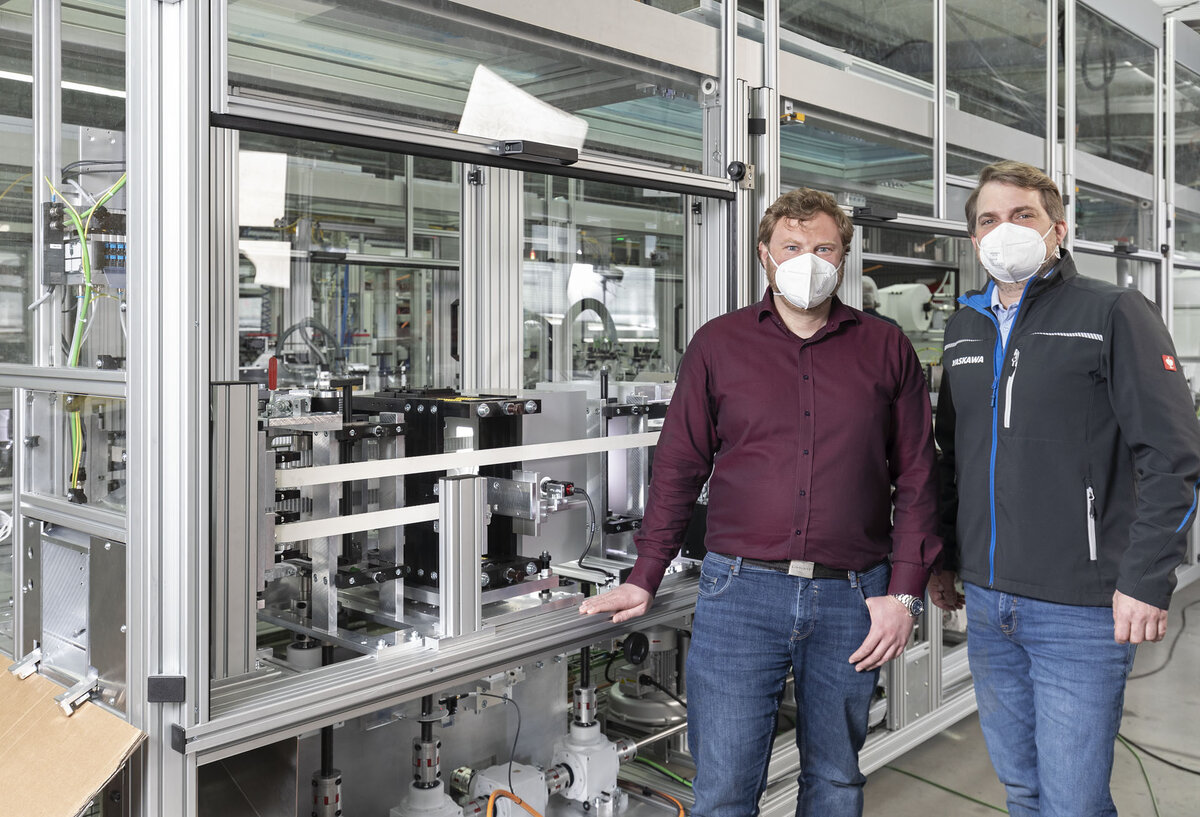
W pełni automatyczny system do produkcji masek ochronnych FFP2
Systemy te są przeznaczone do w pełni automatycznej produkcji masek FFP2 lub KN95 z paskami do mocowania na głowie. Przy długości 10 m, szerokości 1,5 m i wysokości 2 m systemy są bardzo kompaktowe i mogą produkować 40 masek na minutę. Jednak wydajność maszyny jest ograniczona przez długie elastyczne paski. Wielowarstwowy materiał, z którego wykonane są maski, również nie jest łatwy w obróbce. Dlatego materiał jest transportowany przez system ze stałą prędkością. Systemy zgrzewania ultradźwiękowego działają jak latające piły. Specjalne właściwości materiału stawiają tym procesom produkcyjnym wysokie wymagania, które wymuszają zastosowanie wysokowydajnej, precyzyjnie zsynchronizowanej technologii napędowej.
Dostarczenie systemu na rynek w ciągu kilku miesięcy było wyjątkowym osiągnięciem. Harmonogram był napięty, a producent maszyn musiał realizować zamówienie równolegle do swoich codziennych procesów. Prędkość, elastyczność i możliwości programowania również stanowiły poważne wyzwanie. "Przy produkcji masek musieliśmy się zmierzyć z trzema złożonymi zagadnieniami technicznymi: latającą piłą, ultradźwiękową obróbką konturu tłoczenia i technologią cięcia" - wspomina dr Kahlau. "Aby szybko i bezpiecznie znaleźć skuteczne rozwiązanie, zatrudniliśmy kompetentnych partnerów posiadających niezbędną wiedzę. Polegaliśmy w dużej mierze na elastyczności, zwłaszcza w przypadku konieczności podejmowania szybkich decyzji, oraz na gotowości całego zespołu do współpracy zarówno między sobą, jak i z naszymi partnerami w celu ukończenia projektu w możliwie najkrótszym czasie."
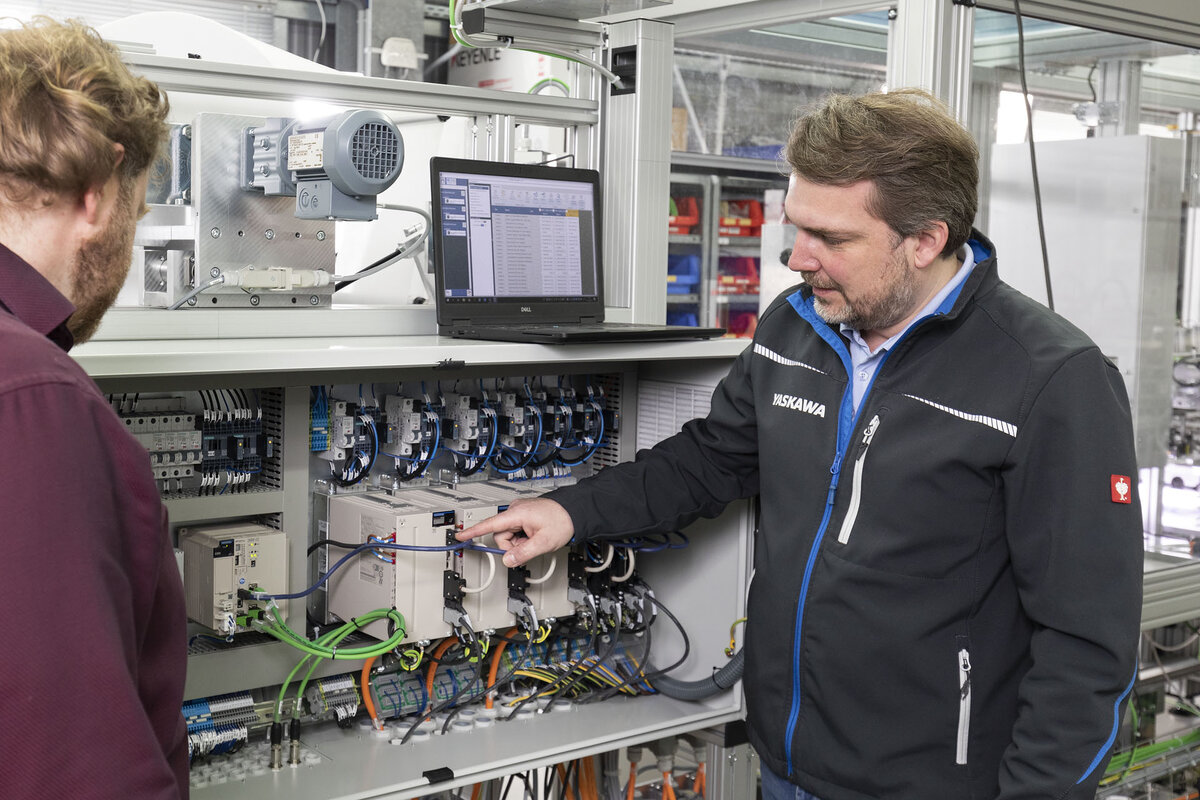
Technologia automatyzacji zapewniająca płynny przebieg procesu produkcyjnego
Podobnie jak w większości swoich systemów, projektanci Unimatic zastosowali sterownik PLC firmy Siemens do sterowania maszyną w systemie produkcji masek. Szukając najlepszego rozwiązania dla płynnej produkcji masek, technicy szybko natrafili na firmę Yaskawa, której sterownik maszyn MP3300iec i serwonapędy Sigma-7 sprawdziły się już w wielu podobnych zastosowaniach i zrobiły wrażenie również na inżynierach. Sterownik posiada już zintegrowane biblioteki funkcji do sterowania krzywką, która może z łatwością realizować funkcję latającej piły. Seria serwonapędów jest synonimem szybkiego rozruchu, wysokiej wydajności produkcji i maksymalnego bezpieczeństwa pracy - wszystkie te cechy były równie ważne dla konstruktorów systemu produkcji masek. Ponadto można było wybierać z szerokiego asortymentu. Seria obejmuje obecnie wąskie moduły wzmacniaczy jedno- i dwuosiowych dla napięć 200 V lub 400 V. Czułe serwonapędy trójfazowe o mocy od 50 W do 15 kW dla napięć zasilania 200 V i 400 V charakteryzują się wyjątkowo kompaktowymi wymiarami i bardzo cichą pracą. Oferują one imponująco wysoką rozdzielczość (zintegrowany 24-bitowy enkoder absolutny), wysoką dynamikę oraz takie funkcje, jak tłumienie drgań, tłumienie częstotliwości rezonansowych maszyny i funkcja automatycznego dostrajania ułatwiająca rozruch. Dzięki zintegrowaniu tych funkcji w serwowzmacniaczach ich wydajność nie jest ograniczona przez kontrolery nadrzędne ani czasy cykli magistrali.
"Jednak nie tylko technologia zrobiła na nas wrażenie" - dodaje Kahlau. "Praca z firmą Yaskawa była niezwykle przyjemna i wszystko przebiegło bezproblemowo. Fachowa pomoc specjalistów ds. automatyki przy projektowaniu napędu, koncepcji sterowania i połączenia ze sterownikiem PLC znacznie przyspieszyła realizację naszego projektu, a gdy tylko pojawiały się jakieś wyzwania, reagowano na nie bardzo szybko. Oferowany przez Yaskawa serwis jest wyraźnym dowodem jakości i kompetencji."
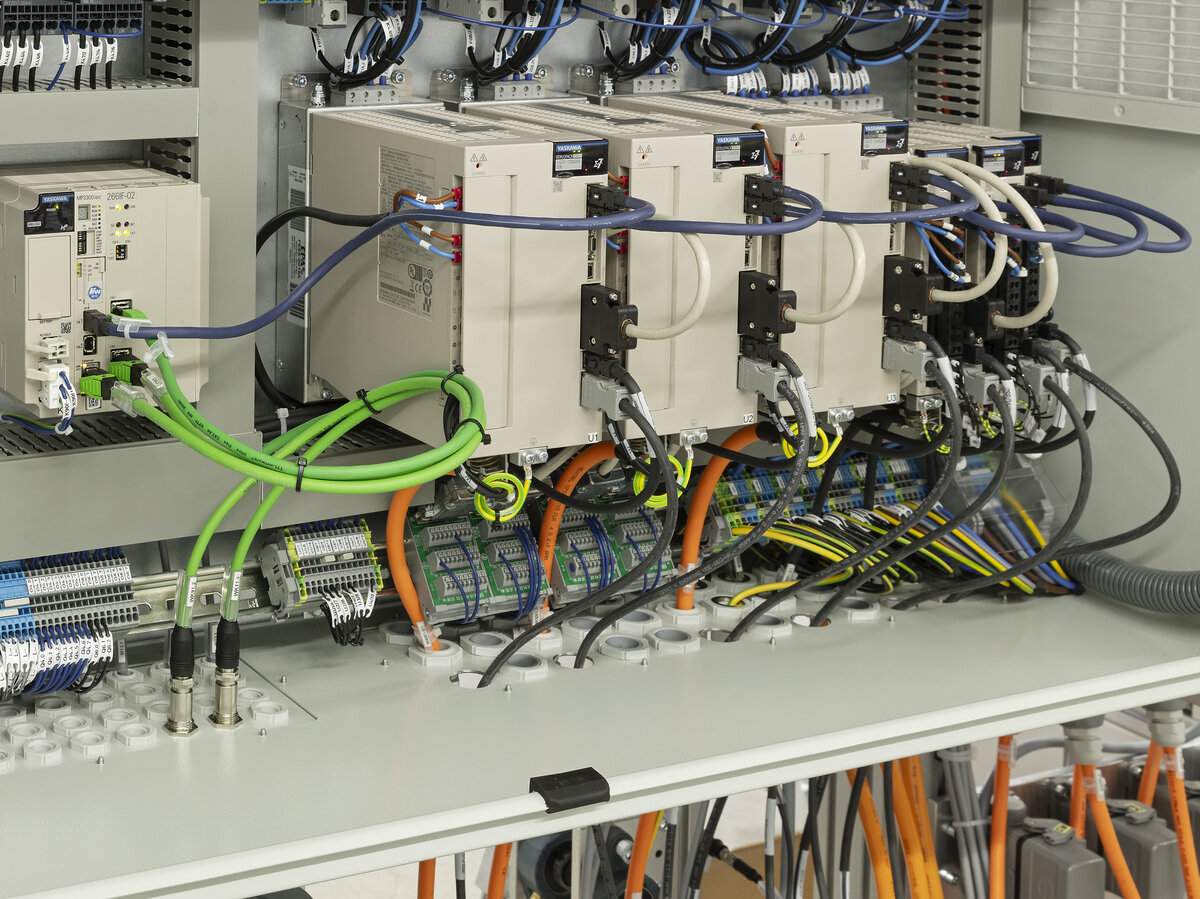
Sześć serwonapędów i sterownik maszyny zapewniają doskonałą synchronizację
W każdym systemie produkcji masek stosowanych jest łącznie sześć serwonapędów Sigma-7 (200 V). Moc silników wynosi od 200 W do 1,5 kW. Największym napędem jest napęd rolek do transportu materiału. Dwa silniki utrzymują dynamiczny ruch latających pił, w tym przypadku narzędzi ultradźwiękowych, które zgrzewają i kształtują maski. Dwa kolejne serwonapędy przygotowują materiał do zawieszenia drucianego klipsa na nosie. Strefa podawania pasków na głowę i klipsów na nos opiera się w dużym stopniu na wysokiej dokładności pozycjonowania i niezwykle precyzyjnej synchronizacji z materiałem.
Synchronizacja serwonapędów w systemie produkcji masek była łatwa do osiągnięcia dzięki zastosowaniu sterownika maszyny MP3300iec. Sterownik komunikuje się z osiami serwonapędów w czasie rzeczywistym za pomocą magistrali Ethernet MECHATROLINK-III - wysokowydajnego interfejsu zaprojektowanego specjalnie dla aplikacji ruchowych. Dzięki szybkości transmisji do 100 Mb/s i czasom cyklu do 125 µs można realizować zadania synchronizacji znacznie bardziej złożone niż w przypadku systemu produkcji masek. Programowanie ułatwia dodatkowo oprogramowanie MotionWorks IEC ze standardowymi blokami funkcyjnymi PLCopen i funkcjami charakterystycznymi dla firmy Yaskawa (np. krzywki i przekładnie elektroniczne), które są dostępne bezpłatnie i które znacznie upraszczają programowanie systemu. Oprócz bloków funkcyjnych PLCopen, MotionWorks IEC zawiera również takie funkcje, jak narzędzia do wizualizacji, systemy kamer, śledzenie przenośników oraz pakiet narzędzi do obsługi G-code. We współpracy ze sterownikiem maszyny bloki funkcyjne umożliwiają również sterowanie kinematyką delta oraz robotami wieloosiowymi.
Sterownik maszyny Yaskawa jest połączony ze sterownikiem PLC systemu produkcji masek za pośrednictwem sieci Profinet. Nadrzędny sterownik PLC nie jest jednak obciążony zadaniem synchronizacji. Sterownik maszyny, który kontroluje wiele obszarów, w tym pneumatykę i bezpieczeństwo, pełni rolę nadrzędną i określa sekwencję oraz cykl pracy napędów. Podczas bieżącej produkcji sterownik ustala punkty wyzwalania. Na przykład, jeśli w danym punkcie systemu wystąpi opóźnienie, synchronizacja dostosowuje się do tego opóźnienia, aby zapobiec przerwaniu produkcji. Rozwiązanie to okazało się bardzo skuteczne. Do tej pory dostarczono i uruchomiono już osiem systemów produkcji masek.