Ponad 100 lat poświęconych postępowi technicznemu - tak najprościej można opisać naszą działalność w zakresie technologii robotycznej i automatyki Yaskawa.
Projekt automatyzacji formowania wtryskowego z wykorzystaniem robotów w pięciu systemach
Aby zaopatrywać klientów posiadających kilka zakładów produkcyjnych na dwóch kontynentach w komponenty hybrydowe z tworzywa sztucznego na czas i w dużych ilościach, wymagane są z jednej strony niezawodne systemy. Najlepszym rozwiązaniem jest produkcja na miejscu pozwalająca utrzymać i zabezpieczyć łańcuchy dostaw tak krótkie, jak to tylko możliwe.
Firma KBS-Spritztechnik musi sprostać dokładnie temu zadaniu i w tym celu wyposażyła pięć wtryskarek w systemy automatyzacji firmy EGS Automation z Donaueschingen.
Trzy z systemów znajdują się w macierzystej fabryce firmy w Schonach w Niemczech, a dwa dodatkowe w zakładzie w Barrie mieszczącym się w Ontario w Kanadzie, który został uruchomiony w 2017 roku. Systemy "pod klucz" zostały opracowane i wdrożone przez firmę EGS Automation z Donaueschingen w okręgu Schwarzwald-Baar. Firma działa w dziedzinie automatyki przemysłowej od 1996 roku, a od 1999 roku wykorzystuje do tego celu roboty przemysłowe. Klienci EGS Automation korzystają z doświadczeń, jakie zdobyła firma, instalując ponad 2 000 robotów, dlatego EGS nazywa siebie firmą robotyczną.
KBS Spritztechnik jest częścią koncernu Burger Group i działa na rynku we ścisłej współpracy z sześcioma innymi markami, co czyni grupę bardzo kompetentnym i silnym dostawcą kompletnego asortymentu dla dostosowanej do potrzeb klienta technologii napędów zębatych. KBS produkuje kompleksowe części z tworzyw sztucznych dla rozwiązań napędowych jako jedno- lub wieloelementowe kombinacje metalu i tworzywa sztucznego lub gumy.
Części formowane wtryskowo, takie jak obudowy, koła zębate, przekładnie ślimakowe, wrzeciona, zębatki czy koła pasowe, należą w równym stopniu do głównych kompetencji firmy, co formowanie wtryskowe złączy, łożysk kulkowych, wałów i kół zębatych z metalu. W ramach zautomatyzowanej produkcji elementów hybrydowych z tworzywa sztucznego produkowane są obudowy dla siłowników mechatronicznych, które są obecnie stosowane w układach wydechowych pojazdów z silnikami spalinowymi oraz w napędach hybrydowych. Komponenty te są produkowane w 12 wariantach. Realizowane są również projekty dla przyszłych pojazdów wyposażonych w alternatywne systemy napędowe.
Proces produkcji jest w pełni zautomatyzowany. Począwszy od dostarczenia złączy wtykowych w postaci wytłoczonej taśmy na zwoju, aż po zapakowanie sprawdzonych wyrobów gotowych w ekologiczne, lekkie i nadające się do recyklingu opakowania wielokrotnego użytku. W każdym systemie zainstalowane są trzy roboty Yaskawa. Dwa małe roboty 6-osiowe zajmują się precyzyjnym doprowadzaniem złączy. Większy robot wyjmuje gotowe części z formy wtryskowej i wkłada dostarczane złącza, a następnie przenosi je do jednostki kontrolnej i do końcowego opakowania. Ponieważ w okresie między dostawą pierwszego i piątego systemu u producenta robotów nastąpiła zmiana generacji z serii MH na serię GP, w systemach stosowane są różne modele. Sprawdzona ciągłość i kompatybilność wsteczna, jak również ciągłość w obsłudze i programowaniu robotów Yaskawa umożliwiły bezproblemową integrację nowej generacji z istniejącą koncepcją zakładu. Zautomatyzowana linia produkcyjna rozpoczyna się od rozwinięcia pasków wykrojów ze zwoju z odpowiednim wyrównaniem i podaniem ich do narzędzia gnąco-wykrawającego.
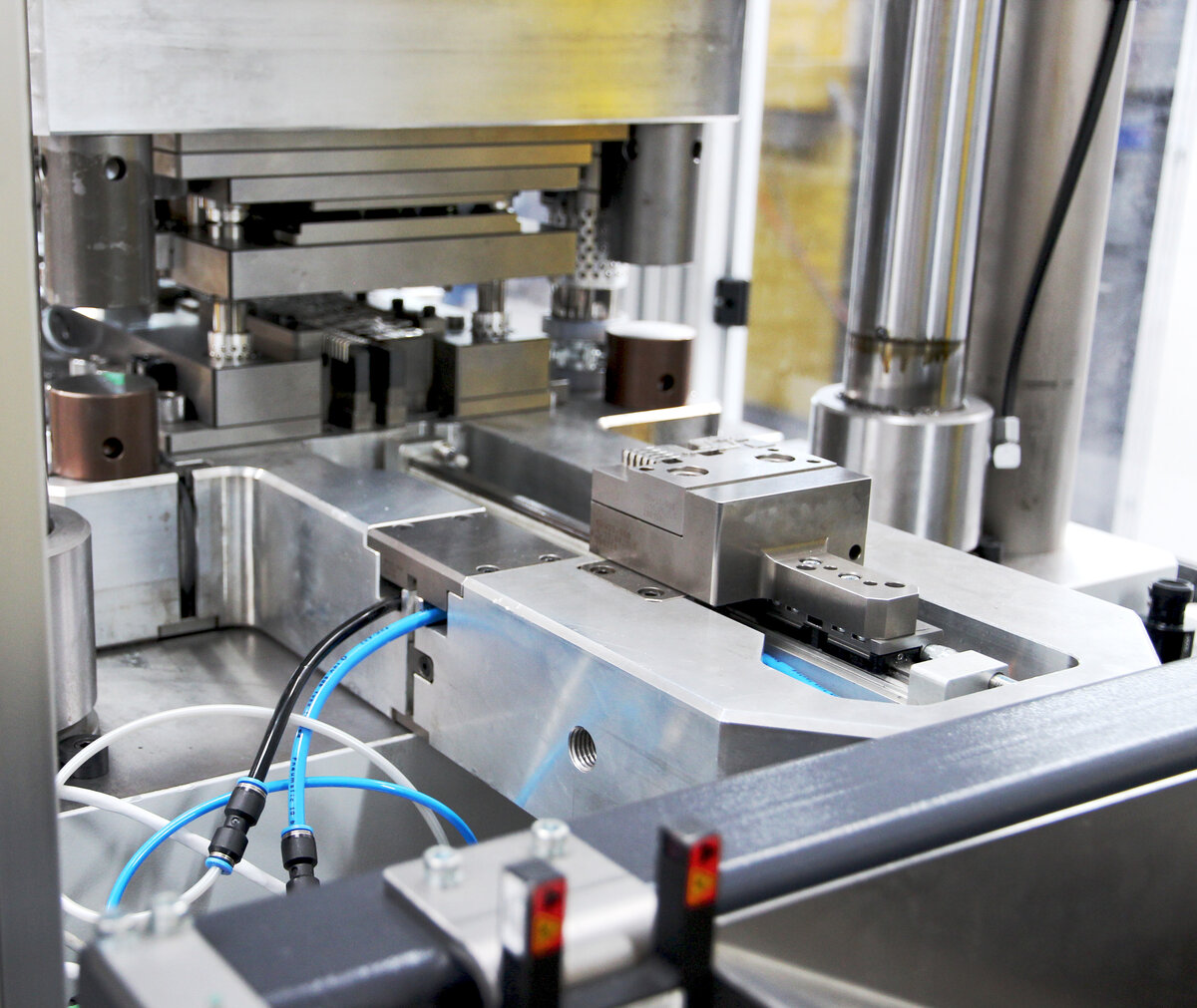
Tutaj złącza są oddzielane, gięte i usuwane przez pierwsze dwa roboty 6-osiowe, a następnie podawane do dwóch stacji, jedno po drugiej, na obrotowym stole indeksującym. Przeprowadzana jest również wstępna kontrola sensoryczna, aby stwierdzić, czy złącza zostały odpowiednio usunięte i czy są wykonane prawidłowo. Udźwig robotów wynosi 7 kg, a ich zasięg to niemal 900 mm.
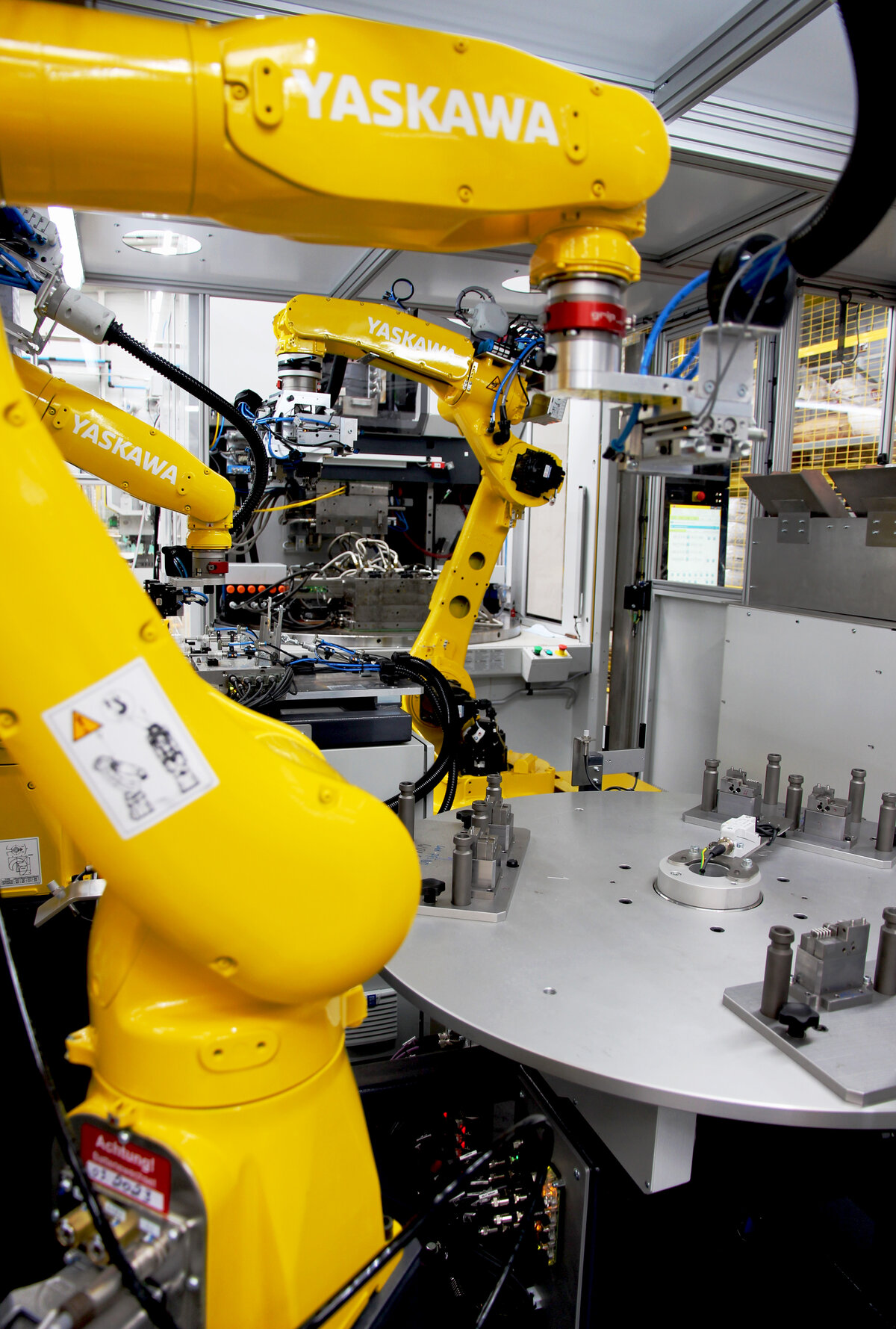
Złącza, które mają być wprowadzone, są dostarczane do 6-osiowego robota firmy Yaskawa o udźwigu 25 kg i zasięgu ponad 1700 m w następnej stacji obrotowego stołu indeksującego we właściwej pozycji w stosunku do ustawienia formy wtryskowej. Wyjmuje on wkłady za pomocą wielofunkcyjnego chwytaka, sprawdza kompletność i przenosi je do wtryskarki - pionowej maszyny Engel o sile zacisku 160 ton. Te maszyny ze stołem obrotowym umożliwiają wyjęcie gotowych części z formy i ponowne załadowanie wkładów, podczas gdy proces formowania wtryskowego przebiega równolegle w drugiej formie o identycznej konstrukcji. W ten sposób prawie całkowicie eliminuje się z cyklu produkcyjnego nakład czasu potrzebny na załadunek i rozładunek przez robota. Jedynie czas obrotu stołu ma tu minimalne znaczenie.
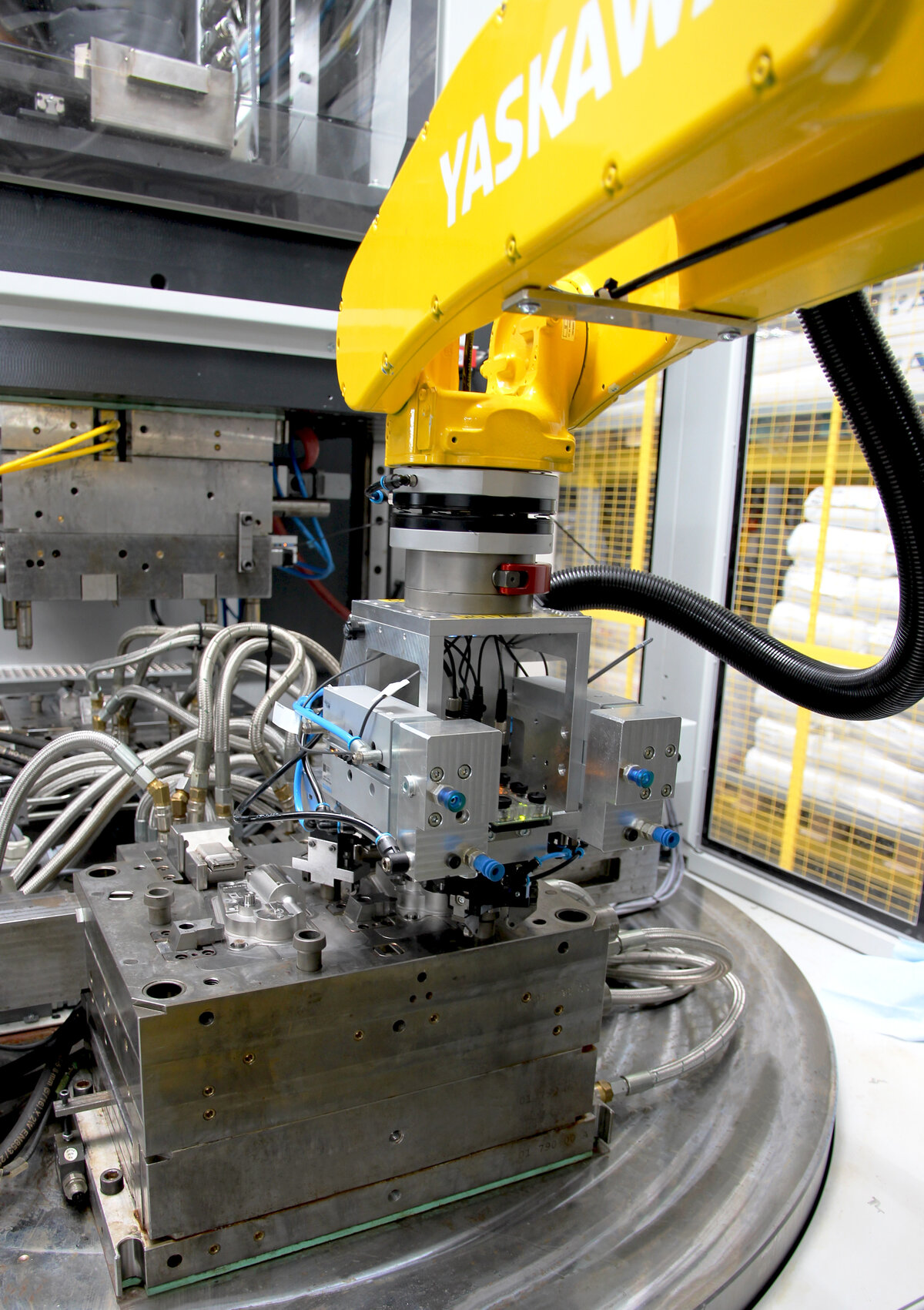
Wszystkie roboty są wyposażone w systemy wymiany za pomocą chwytaków, które umożliwiają szybkie i łatwe przezbrojenie na inne warianty komponentów. Ze względu na ich kompatybilność, chwytaki mogą być stosowane we wszystkich pięciu systemach. Wymienne narzędzia chwytakowe są rozpoznawane za pomocą kodów RFID, a po zakończeniu procesu ustawiania system w pełni automatycznie sprawdza, czy ustawione narzędzia odpowiadają wybranemu wcześniej wariantowi. Formy wtryskowe, jak również narzędzia do wykrawania i gięcia są opracowywane i produkowane w ramach grupy Burger w siostrzanych spółkach SBS-Feintechnik i KBS-Stanztechnik. W zależności od wariantu, gotowe elementy formowane wtryskowo są wyjmowane z formy w 1 lub 2 częściach. Oprócz jednostek funkcjonalnych do obsługi złączy wtykowych i do obsługi gotowych obudów chwytak robota posiada specjalną funkcję umożliwiającą pozycjonowanie elementu podczas wkładania do formy wtryskowej. Aby zapewnić wymaganą wysoką dokładność, EGS Automation wdrożyła specjalną funkcję pozycjonowania dokującego z łożyskami pływającymi, która gwarantuje dokładność i bezpieczeństwo procesu. Po wyjęciu gotowych części są one testowane na stanowisku do prób elektrycznych. Test ciągłości sprawdza połączenie pomiędzy pinami, które muszą mieć łączność elektryczną. Test na przebicie z kolei umożliwia kontrolę, czy podczas procesu formowania wtryskowego w tworzywie sztucznym nie doszło do przypadkowego zetknięcia się ścieżek przewodników, które muszą być elektrycznie odizolowane. Samo stanowisko testowe jest cyklicznie automatycznie ładowane przez robota wzorcowymi wadliwymi częściami, aby zapewnić prawidłowe działanie i w ten sposób zagwarantować klientowi produkty bez wad.
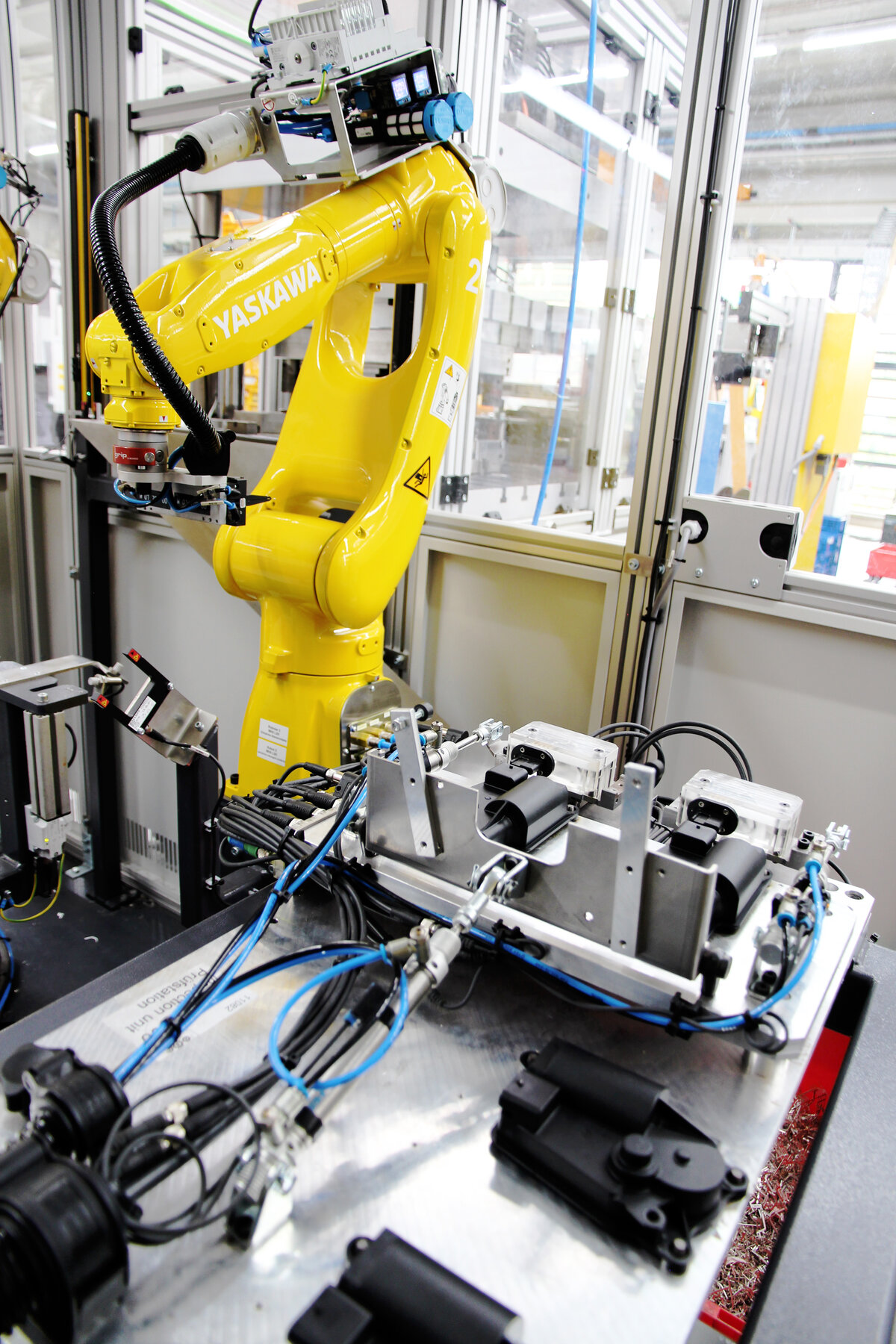
Części wadliwe usuwane są przez odpowiednie zsypy wylotowe. Służą one również do odprowadzenia części gotowych po ponownym uruchomieniu systemu. Na życzenie klienta przez specjalne wyjście mogą być również dostarczane części QA, oddzielone wgłębieniem formy, co umożliwia ciągłe monitorowanie procesu. Na koniec gotowe elementy są pakowane do opakowań klienta. Tacki wielokrotnego użytku w formacie 800 x 600 mm są dostarczane ze stosu bez zawartości przez system paletyzacji wyposażony w podajnik tacek, a następnie układane w stosy z zawartością.
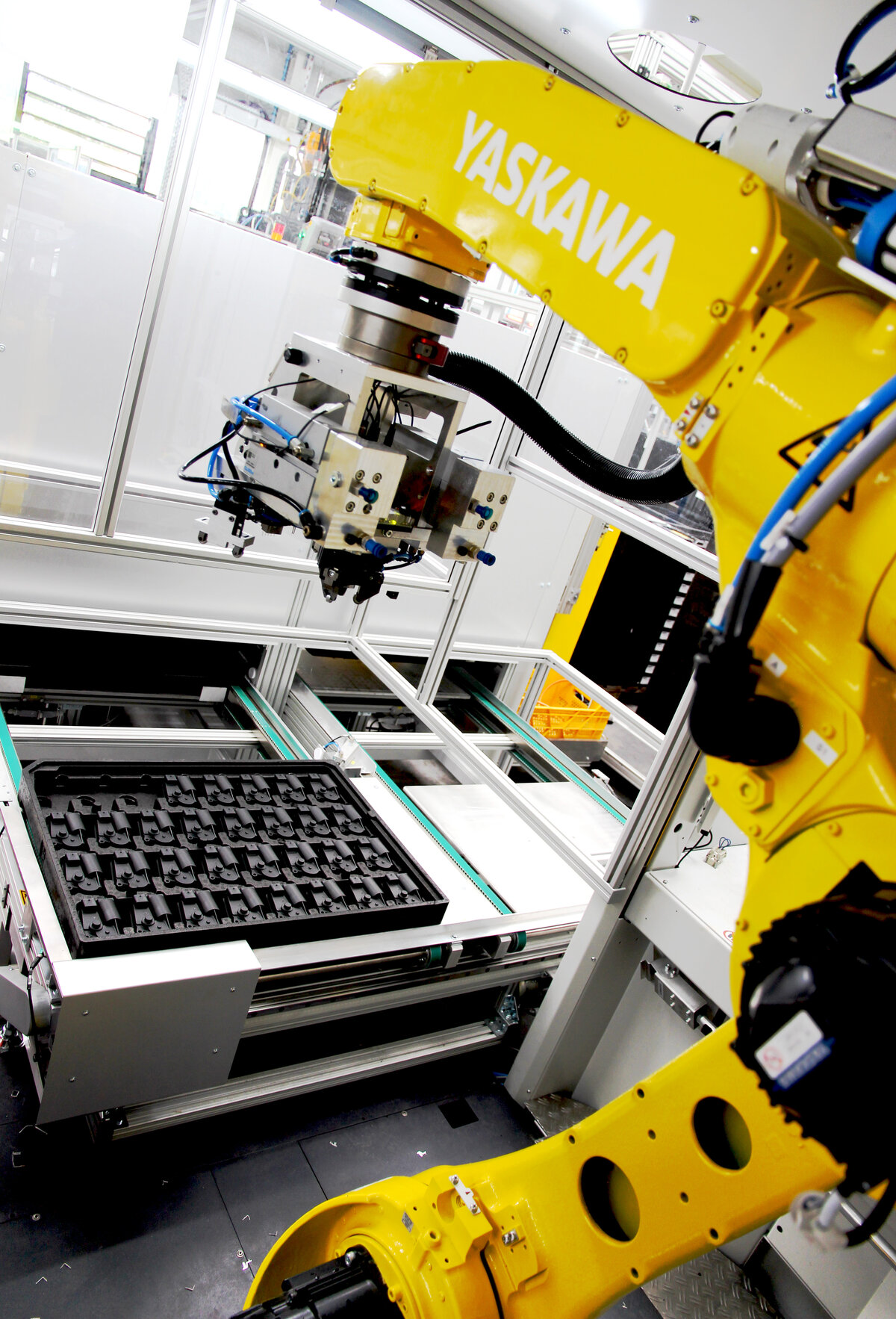
Cała jednostka jest zbudowana jako kompletna i kompaktowa komórka na ramie podstawowej z obudową ochronną i dachem. Już podczas projektowania zwrócono uwagę na możliwość transportu systemów zarówno w kontenerach morskich, jak i w pełni zmontowanych na ciężarówce. To znacznie skraca czas uruchomienia w procesie produkcji na wtryskarce. W jednostkach znajdują się wszystkie elektryczne szafy sterownicze i sterowniki robotów, dzięki czemu zasilanie i doprowadzanie mediów może odbywać się centralnie dla całej instalacji w jednym miejscu. Roboty i poszczególne komponenty są obsługiwane i sterowane za pomocą centralnego systemu sterowania PLC z dużym panelem obsługowym, który służy jako interfejs HMI i umożliwia wygodne wprowadzanie danych oraz monitorowanie stanu. Interfejs użytkownika został zaprogramowany przez EGS Automation zgodnie z określonymi wymaganiami klienta. Thomas Burger, dyrektor zarządzający, jest bardzo zadowolony z koncepcji, realizacji i dostępności systemów.
Zdjęcia: EGS Automation GmbH
Autor:
EGS Automation GmbH
Heiko Röhrig, Leiter Vertrieb u. Marketing
Fon +49 771 898 606 27
Tłumaczenie: Yaskawa Polska