Ponad 100 lat poświęconych postępowi technicznemu - tak najprościej można opisać naszą działalność w zakresie technologii robotycznej i automatyki Yaskawa.
Schneider Weisse automatyzuje proces pakowania z pomocą firmy Profipack i dzięki zastosowaniu robotów Motoman
Eksport wymaga najwyższej elastyczności
Dzięki zastosowaniu tradycyjnej metody warzenia piwa firma Schneider Weisse G. Schneider & Sohn GmbH zapewniła sobie dominującą pozycję na rynku międzynarodowym. Recepta na sukces: metody warzenia stosowane od wieków w średniej wielkości browarze specjalizującym się w produkcji piwa pszenicznego są we wszystkich obszarach wzbogacane o najnowocześniejsze rozwiązania w zakresie automatyzacji. W obszarze logistyki elastyczny system pakowania z trzema robotami Yaskawa Motoman został wdrożony przez specjalistę od systemów pakowania Profipack Verpackungsmaschinen GmbH.
Schneider Weisse G. Schneider & Sohn GmbH (firma założona w 1872 r.) z siedzibą w Monachium i browarem w Kelheim od wielu lat zajmuje się produkcją "piwa rzemieślniczego", jeszcze zanim to modne słowo zaczęło istnieć. Po dziś dzień najlepsze piwne specjały są fermentowane w otwartych kadziach, z których mistrzowie piwowarstwa codziennie, zgodnie z tradycją, ręcznie odcedzają drożdże, a młode piwo osiąga dojrzałość w tradycyjny sposób w butelce lub beczce, zamiast w zamkniętych stalowych zbiornikach.
Przekonujący smak produktu końcowego jest wystarczającym uzasadnieniem dla skomplikowanych procesów technicznych przy produkcji i butelkowaniu. "Stale balansujemy na granicy magii i zaawansowanej technologii" - opisuje obecną sytuację Josef Lechner, główny piwowar w Schneider Weisse. Jako główny technolog Browaru w Kelheim, Lechner jest odpowiedzialny za jedno i drugie, tzn. nie tylko za "magię" warzenia piwa, ale także za niezbędne wyposażenie, czyli instalację systemu odpowiadającego najnowszemu stanowi techniki.
Eksport jako "bodziec" dla wprowadzenia nowej linii pakowania
W październiku 2021 roku Josef Lechner i jego koledzy oddali do użytku nową linię pakującą. Po dwudziestu latach pracy poprzedni system po części tylko zautomatyzowany był przestarzały i należało go wymienić. Zamiast zwykłej reinwestycji, osoby decyzyjne w Schneider Weisse wykorzystały tę okazję do wdrożenia systemu w całkowicie nowej konfiguracji. W ostatnich latach nastąpiły zmiany nie tylko w zakresie możliwości technicznych, ale także podstawowych parametrów w przemyśle piwowarskim.
"Rozszerzenie naszej działalności eksportowej było niewątpliwie czynnikiem sprzyjającym wprowadzeniu systemu w jego obecnym kształcie" - wspomina główny technolog browaru Lechner. Podstawowe różnice w porównaniu z produkcją przeznaczoną na rynek krajowy to małe partie z etykietami dostosowanymi do danego kraju oraz zróżnicowane rodzaje beczek, w przeciwieństwie do wciąż dominującej w Niemczech skrzynki zwrotnej. A sektor sprzedaży detalicznej coraz częściej domaga się mniejszych beczek. "Ogólnie rzecz biorąc, rynek piwowarski nabrał szybkiego tempa" - podsumowuje ekspert branżowy i dodaje: "Innymi słowy: musimy również szybciej reagować". Centralnym wymogiem przy planowaniu nowego systemu była więc najwyższa elastyczność - zarówno w bieżącej działalności, jak i z myślą o rozbudowie w przyszłości.
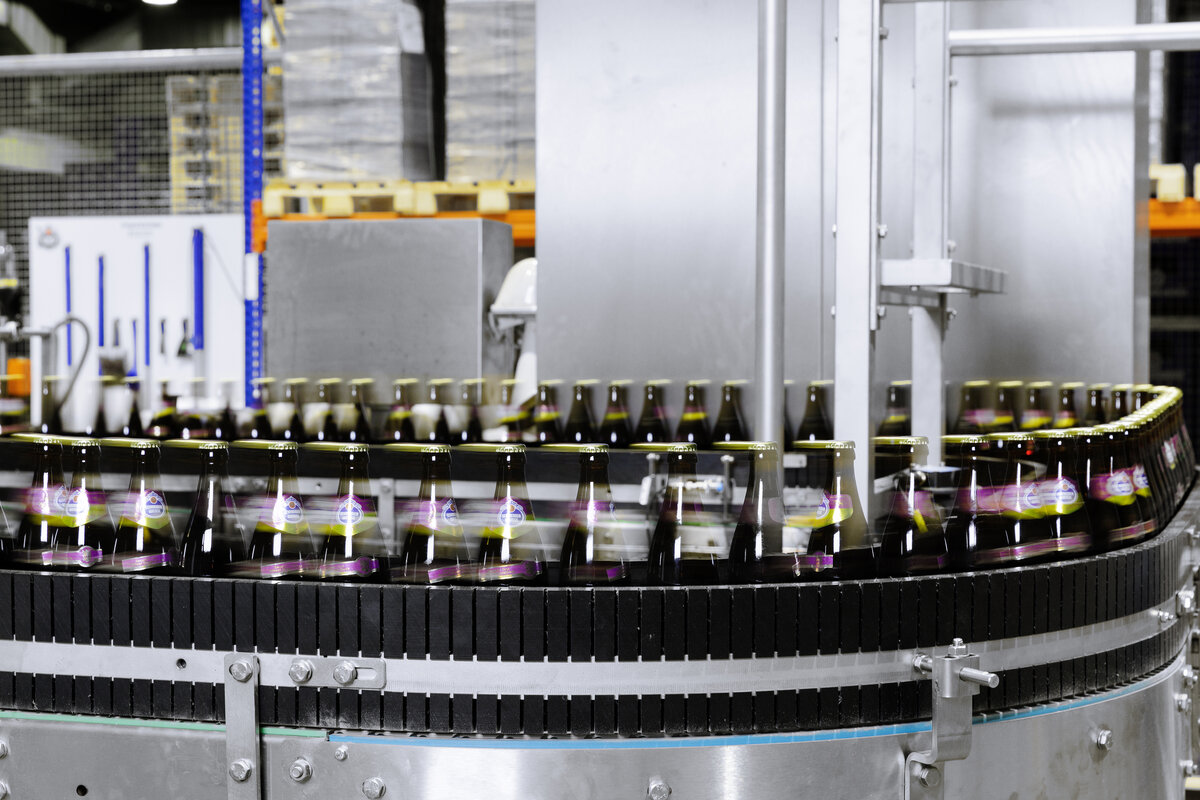
Koncepcja systemu z robotami przemysłowymi
Idealne rozwiązanie zostało opracowane przez Schneider Weisse we współpracy z Profipack Verpackungsmaschinen GmbH. Ta założona w 1998 roku firma ze Schwoich, niedaleko Kufstein, specjalizuje się w technice pakowania, paletyzacji, rozładunku i transportu, jak również w systemach intralogistycznych w tym zakresie - nie tylko dla obszarów przemysłu spożywczego i napojów. "To spojrzenie z zewnątrz było dla nas jako browaru poszukującego nowych dróg bardzo przydatne", Josef Lechner chwali kompetencje Tyrolczyków.
Peter Niederacher, dyrektor techniczny i dyrektor generalny w Profipack, pamięta pierwszą wersję projektu systemu, którą nakreślił: "Układ spotkał się z pozytywną reakcją, ponieważ system był bardzo dobrze zorganizowany, zajmował niewiele miejsca, a jednocześnie był optymalnie dostępny". Jedną z mocnych stron Profipack jest projektowanie systemów zgodnie z zasadą złotego środka: "Tak mało jak to możliwe, tak dużo jak to konieczne".
Około 95% linii pakującej zostało zrealizowane zgodnie z tym pierwszym projektem. Wykorzystano w niej roboty przemysłowe - dotychczas niezbadany obszar dla zakładu piwowarskiego Schneider Weisse w Kelheim. Zapewniają one wymaganą elastyczność przy minimalnej fragmentaryzacji na ograniczonej przestrzeni. Niederacher opisuje koncepcję systemu w następujący sposób: "Połączyliśmy rozładunek i rozpakowywanie w jednej celi robotycznej. Dzięki temu oszczędzamy dużą ilość miejsca i minimalizujemy ilość sprzętu potrzebnego do obsługi. Personel obsługujący ma również optymalny dostęp do urządzenia i czerpie korzyści z krótkich dystansów."
Nowa linia pakowania działa niezależnie od głównej rozlewni. Wózki widłowe dostarczają nieoznakowane butelki w skrzyniach z magazynu pośredniego i odbierają załadowane palety. Pomiędzy tymi dwoma procesami znajduje się cała seria automatycznie wykonywanych operacji, w których główne zadania są wykonywane przez trzy roboty. Pierwszy robot rozładowuje produkt, w tym samym kroku usuwając butelki ze skrzynek i odkładając je na bok. System przekłada butelki do skrzynek lub pudełek. W zależności od zastosowania, puste skrzynki są przekazywane do maszyny pakującej lub ponownie układane na palecie, a butelki trafiają dalej do maszyny etykietującej. Po etykietowaniu drugi robot pakuje butelki do skrzynek lub pudełek. System ten również zamyka i etykietuje skrzynki. Wreszcie trzeci robot umieszcza gotowe do wysyłki wypełnione pudełka lub skrzynki na różnego rodzaju paletach.
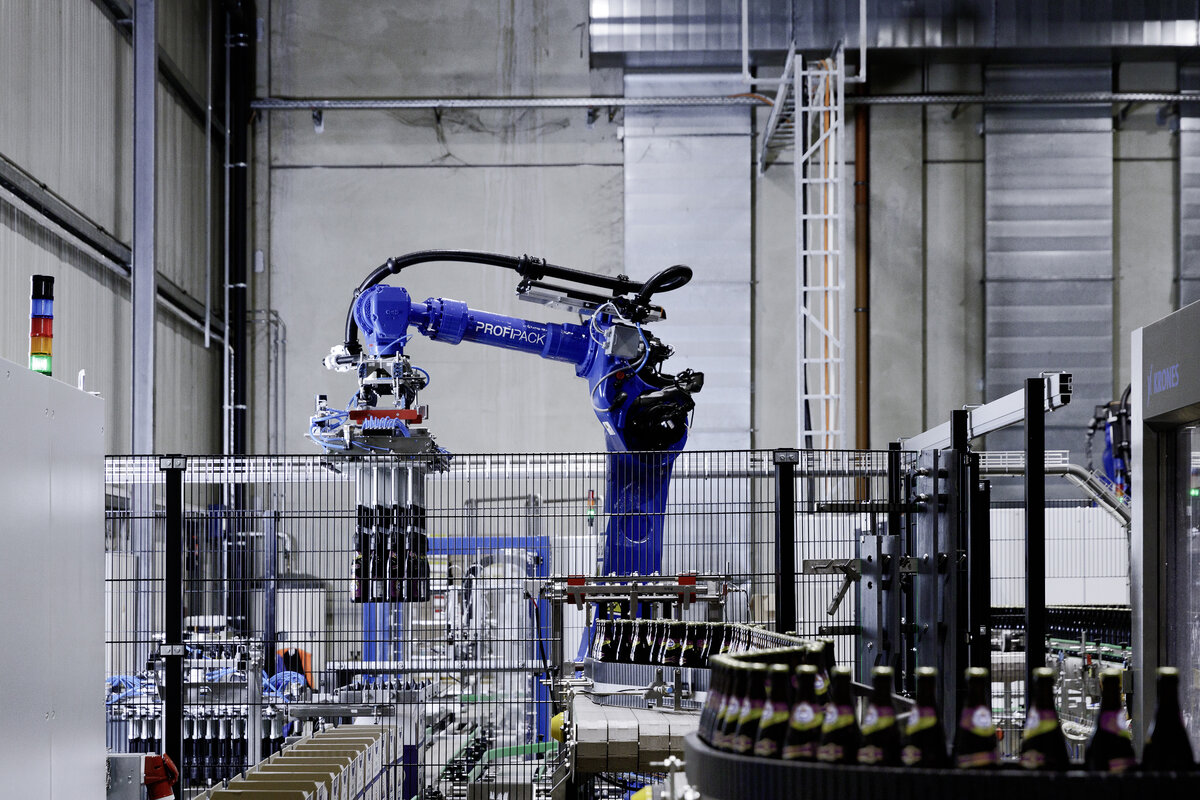
Seria Motoman GP
Wszystkie trzy roboty to modele z serii Motoman GP. Dla Niederachera i jego współpracowników decyzja o wyborze firmy Yaskawa była jasna od samego początku. Decyzję tę tłumaczy on następująco: "Profipack używa robotów Motoman od 2004 roku i dlatego jesteśmy przekonani o ich jakości technicznej, a także o bezproblemowej współpracy i wsparciu".
W systemie pracują trzy roboty Motoman GP180, każdy o udźwigu 180 kg. "GP" to skrót od "general purpose" i oznacza, że są one odpowiednie do różnych zastosowań. 6-osiowe roboty spełniają wysokie wymagania klasy ochrony IP67, dzięki czemu są szczególnie odporne na przenikanie cieczy i pyłu. Mogą być stosowane w trudnych warunkach pracy i są łatwe w czyszczeniu.
Każdy z trzech robotów jest sterowany przez wysokowydajny kontroler YRC1000, który jest zintegrowany w systemie z nadrzędnym sterownikiem PLC S7-1500 poprzez sieć Profinet. Jeden robot jest wyposażony w chwytak do załadunku i rozładunku butelek i skrzynek. Druga cela robotyczna wykorzystuje chwytaki do butelek o odpowiednich kształtach i może być rozbudowana o chwytak do koszy i opakowań typu clusterpack. Trzeci robot wykorzystuje głowicę paletyzującą do pudełek i skrzynek. Cały system umożliwia przestawienie na butelki 0,33 (LN) lub 0,5 litra (NRW i EURO) w czasie krótszym niż 15 minut. W chwytakach robota zastosowano system automatycznej wymiany narzędzi.
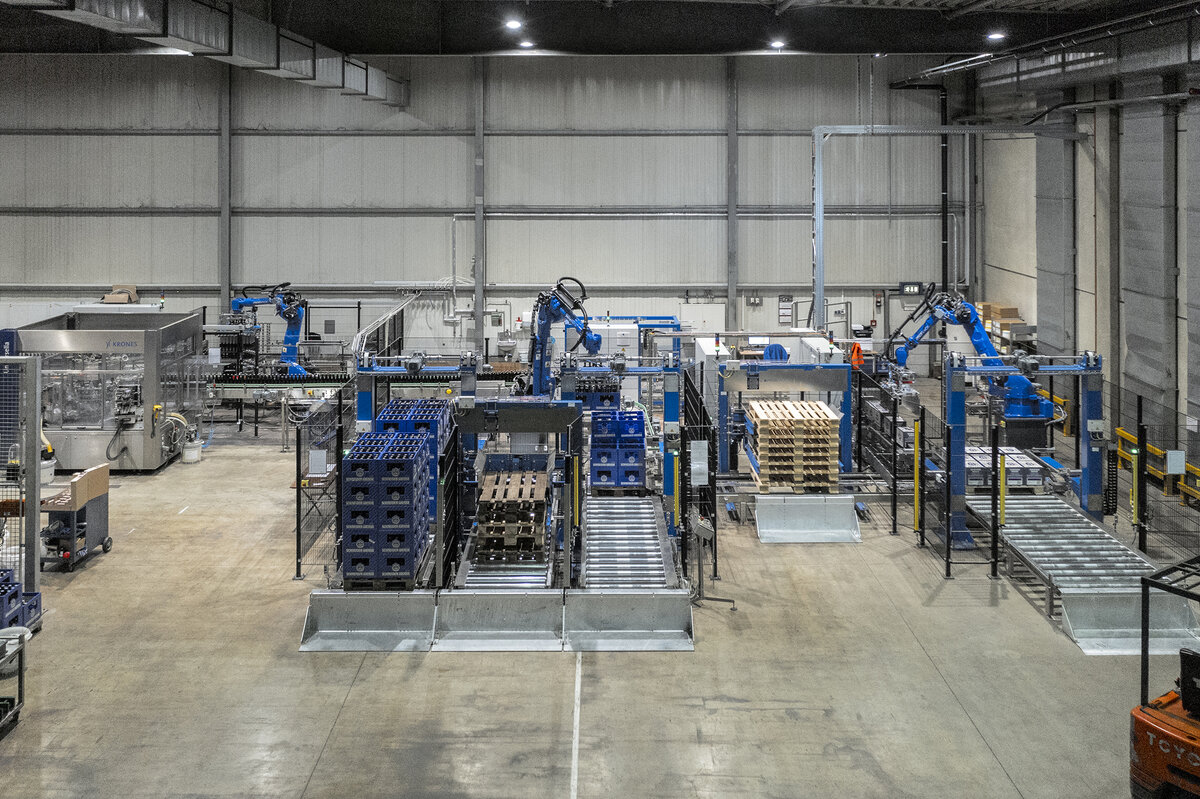
Rozbudowa możliwa w każdej chwili
Po pierwszych sześciu miesiącach użytkowania w praktyce mistrz browaru Josef Lechner jest całkowicie zadowolony z nowej linii pakującej: "Wszystko przebiega sprawnie i bezproblemowo! Pozostaje tylko pytanie, w jaki sposób możemy dalej wykorzystać wydajność produkcyjną instalacji." Modułowa rozbudowa z pomocą Profipack do opakowań typu clusterpack i koszy (takich jak sześciopaki) była również rozważana jako opcja.
Autor:
Sepp Hautzinger (Sales Manager Robotics Division)
Yaskawa Europe GmbH – Sales Office Austria, AT-Schwechat/Wien
Kontakt:
Yaskawa Europe GmbH
D-85391 Allershausen
Tel. +49-8166-90-0
Fax +49-8166-90-103
Profipack Verpackungsmaschinen GmbH
A-6334 Kufstein
Tel.: +43-5372-64747
Fax: +43-5372-64747-47
Tłumaczenie: Yaskawa Polska
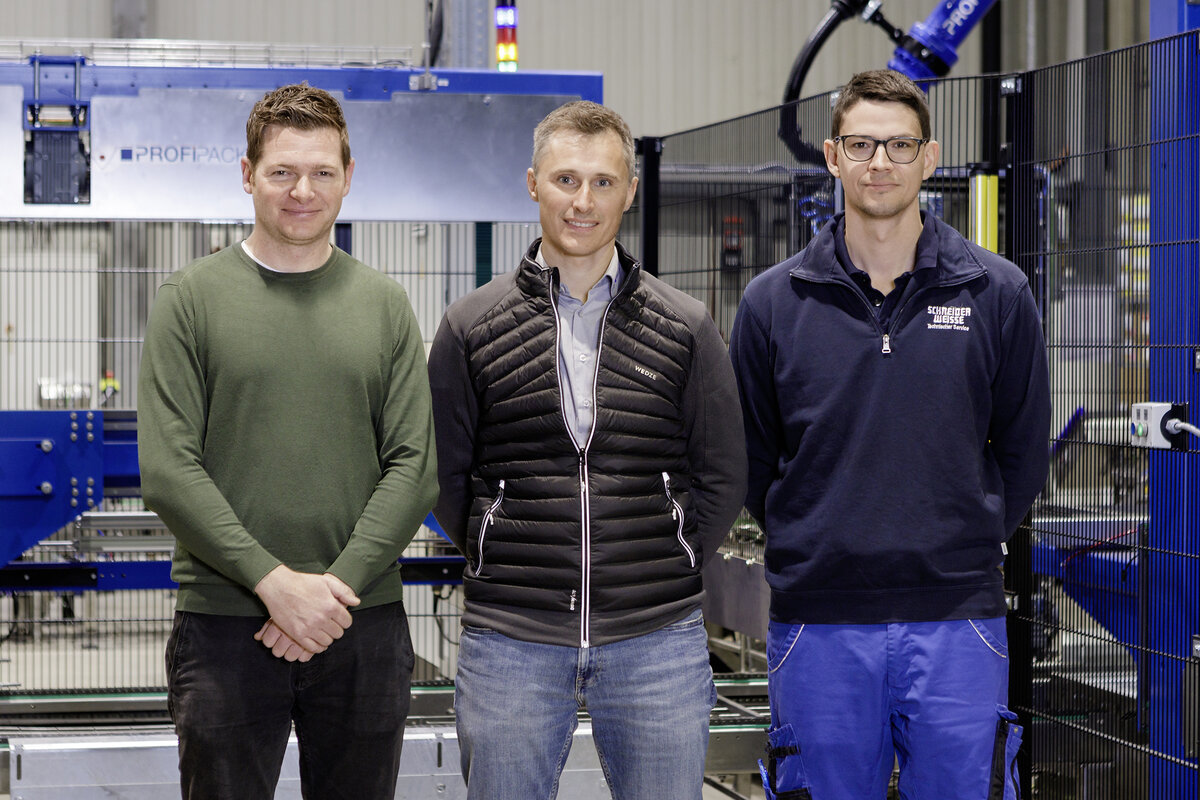