Ponad 100 lat poświęconych postępowi technicznemu - tak najprościej można opisać naszą działalność w zakresie technologii robotycznej i automatyki Yaskawa.
Zaawansowana automatyzacja produkcji na poziomie kilku milionów złączy
Inteligentne połączenie i konsekwentna automatyzacja
Jak poradzić sobie ze stale rosnącym zapotrzebowaniem na elementy hybrydowe z tworzywa sztucznego pomimo ograniczeń przestrzennych i personalnych? Międzynarodowy dostawca z branży motoryzacyjnej zdecydował się na zastosowanie systemu z dwoma wtryskarkami i sześcioma robotami, co okazało się bardzo korzystne.
Zatrudniająca około 3000 pracowników na całym świecie firma KE Elektronik jest jednym z najbardziej cenionych dostawców przemysłu motoryzacyjnego i lotniczego. Firma posiada zakłady produkcyjne w Niemczech, Czechach, Słowacji, północnej Macedonii, Chinach i Meksyku i należy do amerykańskiego koncernu Amphenol Corporation będącego wiodącym producentem złączy.
Od pewnego czasu wśród produktów wytwarzanych przez firmę w jej siedzibie w Kressberg-Marktlustenau znajdują się złącza wentylatorów silnika, które są stosowane zarówno w pojazdach hybrydowych, jak i tych napędzanych wyłącznie przez silniki spalinowe. Złącza te to tzw. elementy hybrydowe z tworzywa sztucznego, w których cztery metalowe styki są obtryskiwane trzema różnymi rodzajami tworzywa sztucznego.
"Produkcja tych złączy jest stosunkowo złożonym procesem, który obejmuje liczne etapy testowania, jak również możliwość zapewnienia pełnej identyfikacji produktu. Aby móc sprostać stale rosnącemu zapotrzebowaniu, biorąc pod uwagę niedobór wykwalifikowanych pracowników, konieczne było przemyślane rozwiązanie z zakresu automatyzacji" - mówi Jens Gradenegger, kierownik zespołu ds. automatyzacji formowania wtryskowego w KE Elektronik.
Wyjątkowo wymagający projekt
Firma KE Elektronik zwróciła się do EGS Automation GmbH
w Donaueschingen z prośbą o podjęcie się zadania zautomatyzowania i połączenia dwóch modułów do wykrawania i gięcia oraz dwóch wtryskarek Arburg tak, aby powstała w ten sposób jednostka produkcyjna mogła osiągnąć wydajność kilku milionów złączy rocznie. "Nasze dotychczasowe doświadczenia ze współpracy z EGS były jak najbardziej pozytywne, więc mieliśmy pewność, że i w tym przypadku będą w stanie zaoferować nam niezawodne rozwiązanie", mówi Jens Gradenegger.
Firma EGS nie byłaby sobą, gdyby nie zaproponowała idealnego rozwiązania do wykonania tego skomplikowanego zadania. "Lubimy potwierdzać nasze kompetencje, podejmując się ambitnych projektów, a ten z pewnością dał nam ku temu okazję. W ścisłej współpracy z KE udało nam się zaprojektować wyspę produkcyjną o wymiarach 15 x 6 metrów z sześcioma robotami Motoman firmy Yaskawa, dużą ilością urządzeń obsługujących i testowych oraz systemem paletyzacji SUMO Ecoplex2, która spełnia wszystkie wymagania" - mówi kierownik projektu EGS Hartmut Pfalzgraf.
Cała linia produkcyjna została wyraźnie podzielona na cztery moduły, a przejrzystość rozmieszczenia poszczególnych elementów robi wrażenie. W celu spełnienia wymagań dotyczących czasu cyklu poniżej dziesięciu sekund na złącze, jak również maksymalnej dostępności, zastosowano wyłącznie komponenty najwyższej jakości. Zadbano również o zapewnienie dobrej dostępności we wszystkich częściach systemu. A oto jak system wygląda w praktyce:
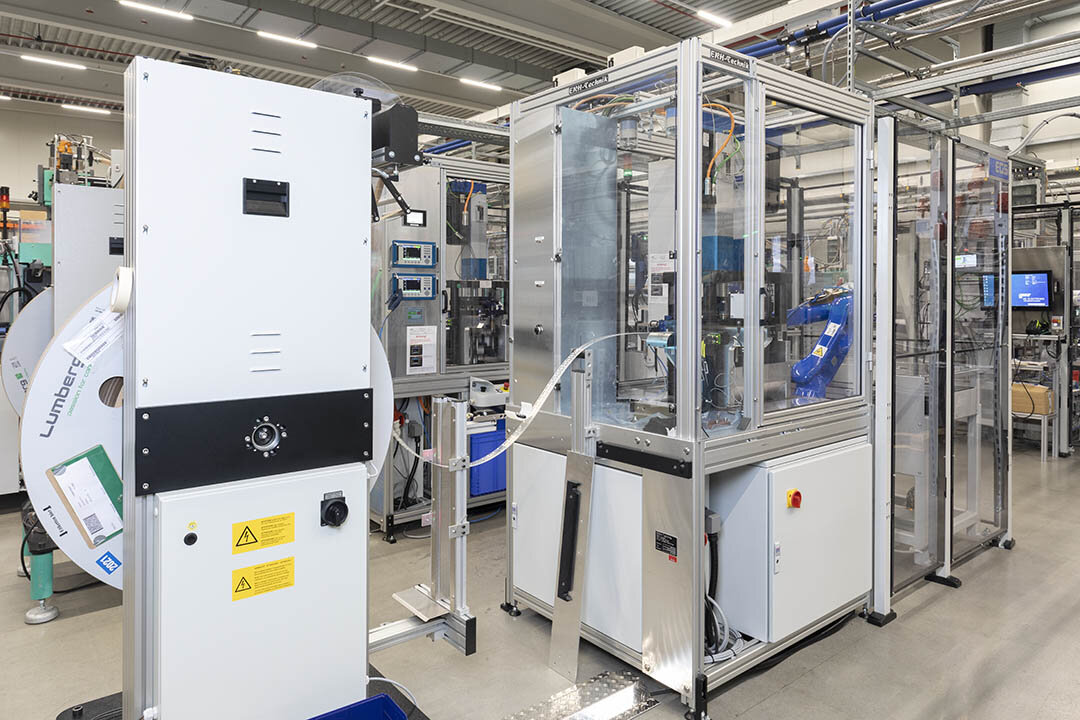
Moduł I: przygotowywanie styków złącza
Dwie jednostki wykrawająco-gnące zapewniają nieprzerwane dostarczanie styków złącza. Podczas gdy jedna linia wytwarza piny sygnałowe, druga wytwarza piny zasilające. Na każdej jednostce wykrawająco-gnącej zainstalowany jest robot MOTOMAN GP7 z chwytakiem mechanicznym wyposażonym w technologię czujników i pochylony o 25 stopni. "Pochylona pozycja robota pozwala nam wykonać obrót z pozycji wyjmowania do pozycji wstawiania elementu wyłącznie za pośrednictwem osi S, co pozwala na skrócenie czasu cyklu do minimum" - mówi Hartmut Pfalzgraf. To genialne rozwiązanie inżynieryjne, które odzwierciedla doświadczenie firmy EGS obejmujące ponad 2000 instalacji robotów.
Dwa roboty 6-osiowe wyjmują po dwa styki ze swojej linii i umieszczają je w nośniku przedmiotu obrabianego z czterema gniazdami, z których każde musi być obsadzone czterema stykami. Po czterech cyklach roboczych dwa roboty 6-osiowe całkowicie obsadzają cztery gniazda, a nośniki przedmiotów obrabianych osiągają pozycję rozładunkową i są zabierane przez MOTOMAN GP50 do modułu II.
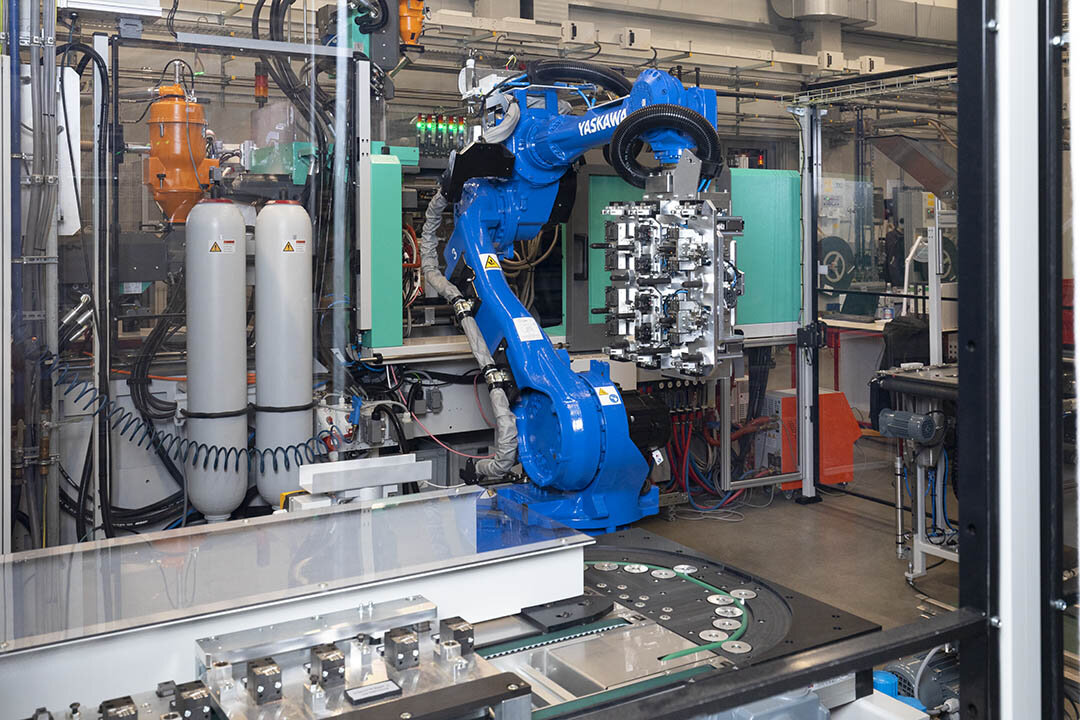
Moduł II: złożone procesy obsługi za pomocą GP50
Sercem modułu II jest wtryskarka dwukomponentowa firmy Arburg, na której przetwarzane są jednocześnie dwa rodzaje tworzyw sztucznych. W pierwszym kroku, za pomocą górnej formy SGM, wykonywane jest obtryskiwanie styków w celu ich precyzyjnego zamocowania w żądanej pozycji. Powstałe w ten sposób nośniki styków są następnie obtryskiwane na wtyczce w drugim cyklu za pomocą dolnej formy wtryskowej.
Za wszystkie procesy załadunku i rozładunku SGM odpowiedzialny jest 6-osiowy robot MOTOMAN GP50 firmy Yaskawa, na którym zamontowany jest system potrójnych chwytaków o masie 36 kg. Dzięki zasięgowi 2061 milimetrów i udźwigowi 50 kg robot ten doskonale nadaje się do tego zadania. Zakres zadań wykonywanych przez 6-osiowego robota jest bardzo złożony.
Najpierw robot musi rozładować maszynę SGM, zanim będzie mógł wyposażyć ją w nowe styki. Aby to zrobić, musi usunąć gotowe złącza z dolnej formy, przenieść wstępnie uformowane części z górnej formy do dolnej formy i w końcu wyposażyć pustą górną formę w wykrojone i zagięte styki 4x4 z nośnika przedmiotów obrabianych z modułu 1.
"Aby osiągnąć wymaganą precyzję podczas chwytania, robot przed właściwym przeładunkiem dokuje formy za pomocą chwytaka centrującego. W celu maksymalnego skrócenia czasu otwarcia formy wykorzystujemy wzorcową dynamikę robota GP50", mówi Jens Gradenegger.
Na koniec uformowane metodą obtryskiwania złącza są umieszczane na kolejnym nośniku przedmiotów obrabianych. Z ośmioma złączami nośnik przedmiotów obrabianych jest przenoszony z modułu II do modułu III za pomocą systemu transferowego.
Moduł III: obtryskiwanie ciekłym silikonem (LSR)
Istotnym etapem procesu w module III jest obtryskiwanie złączy LSR, które również odbywa się na wtryskarce firmy Arburg. Zaletą jest to, że dzięki obtryskiwaniu złączy z silikonową krawędzią nie jest wymagana osobna uszczelka, a więc nie ma potrzeby stosowania dodatkowego elementu, który mógłby powodować problemy podczas montażu.
Moduł III również wykorzystuje robota MOTOMAN GP50, ale jego praca nie jest tak skomplikowana jak jego „kolegi” w module II. Tutaj robot wyjmuje złącza 2x4 z nośnika przedmiotów obrabianych i sprawdza ich temperaturę, trzymając je przed kamerą termowizyjną. Dopiero gdy temperatura mieści się w określonym przedziale, detale nadają się do kolejnego procesu wtryskiwania i robot umieszcza je w formie.
Również w tym przypadku pierwszym krokiem przed załadowaniem wtryskarki jest usunięcie ośmiu gotowych części. Następnie GP50 ładuje podwójny transporter, który zabiera łącznie 16 elementów do ostatniego modułu.
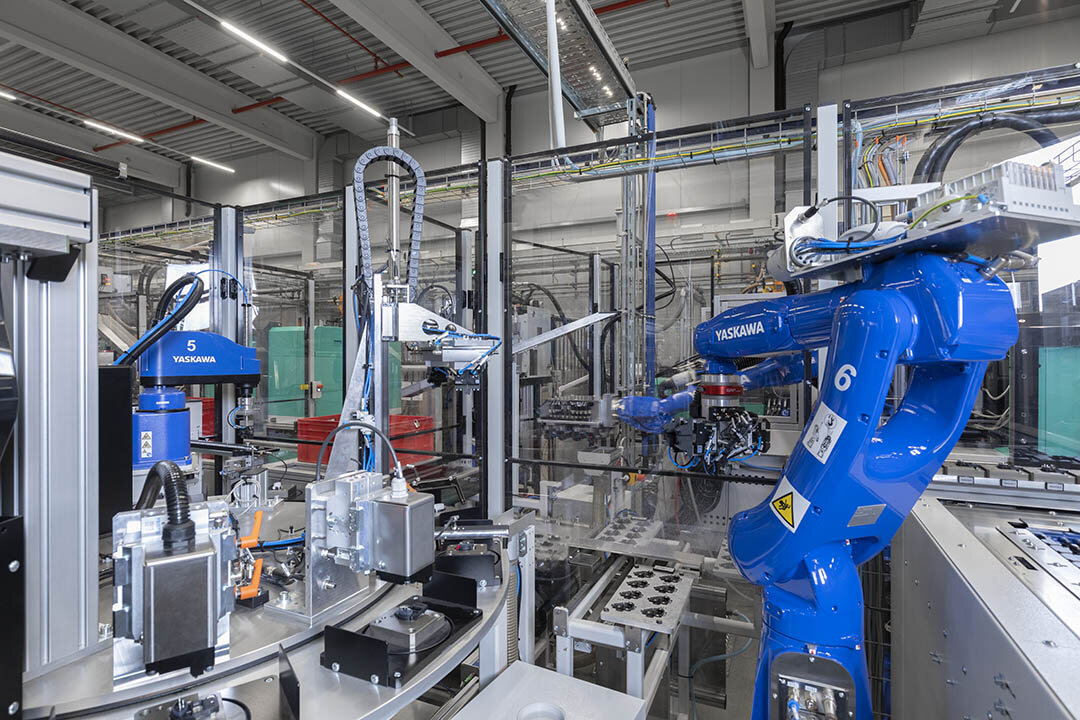
Moduł IV: testy, testy, testy
Do pracy w module IV wykorzystywany jest kolejny robot MOTOMAN GP7, którego zadaniem jest odbieranie gotowych części i przenoszenie ich do obrotowego zespołu transferowego. "Na tej obrotowej jednostce znajdują się różne stanowiska testowe oraz stanowisko montażowe wyposażone w robota MOTOMAN SG650 Scara. Udało nam się tutaj zintegrować naprawdę dużą liczbę procesów na niezwykle małej przestrzeni" - mówi Jens Gradenegger.
Ten moduł służy przede wszystkim zapewnieniu jakości. W pierwszej kolejności przeprowadzany jest test ciągłości i wysokiego napięcia, następnie sprawdzane jest położenie pinów za pomocą lasera triangulacyjnego, po czym następuje kontrola obtrysku LSR przy użyciu kamery, a następnie laser znakujący nadaje elementowi kod matrycy danych, zapewniając w ten sposób stuprocentową identyfikację.
Gdy komponent pozytywnie przejdzie cały szereg testów, ostatnim etapem jest sterowany momentem obrotowym montaż osłony ochronnej, który wykonuje robot SG 650 Scara. "Bardzo dużym atutem okazał się tutaj fakt, że Yaskawa już od jakiegoś czasu oferuje roboty 4-osiowe. Dzięki temu mogliśmy wyposażyć całą instalację w roboty jednego producenta i jednocześnie pozostać przy firmie Yaskawa w zakresie wyboru układu sterowania" - mówi Jens Gradenegger.
Robot Scara nie jest wykorzystywany do granic możliwości, ale w przypadku MOTOMAN GP7 sytuacja wygląda inaczej: "ten 6-osiowy robot ma decydujące znaczenie dla czasu cyklu, ponieważ nie tylko ładuje obrotową jednostkę transferową, ale także finalizuje proces, umieszczając gotowe elementy na tacach w SUMO Ecoplex2 - najlepiej sprzedającym się systemie paletyzacji EGS. Dołożyliśmy wszelkich starań, aby nie przekroczyć założonego czasu cyklu. Robot jest wyposażony między innymi w system chwytaków 2+2, co pozwala zmniejszyć liczbę ruchów", mówi Hartmut Pfalzgraf.
Od września 2021 roku zakład pracuje na trzy zmiany, a wdrożone rozwiązanie w pełni spełnia oczekiwania KE, jak zapewnia Jens Gradenegger: "Firma EGS rzeczywiście wykonała znakomitą pracę - od planowania aż po uruchomienie. Mogliśmy skorzystać z fachowej wiedzy konstruktorów EGS w zakresie wszelkiego rodzaju szczegółowych rozwiązań. Do tego należy dodać tradycyjną niezawodność robotów Yaskawa, którą szczególnie cenimy u nas w KE."
Text: Ralf Högel