Ponad 100 lat poświęconych postępowi technicznemu - tak najprościej można opisać naszą działalność w zakresie technologii robotycznej i automatyki Yaskawa.
Görtz bakery to rely on robots in future with ADM and Yaskawa
High performance in a limited space
ADM has made a name for itself in this industry with intelligent automation solutions for industrial bakeries. The machine and system manufacturer from Warburg in eastern Westphalia is firmly committed to Yaskawa MOTOMAN robots. This is also the case with an ongoing project for the Ludwigshafen bakery Görtz, where four robots handle frozen dough within a very constricted space.
In its current industry report [1] the Association of German Industrial Bakers states: “Fewer and fewer bakeries are selling more and more baked goods”. This means that individual companies must increasingly expand their production capacities in order to remain competitive. In view of the shortage of personnel in the food industry, automation is becoming even more important for large-scale bakery production.
Görtz Bakery breaks new ground
Bäckerei Görtz GmbH in Ludwigshafen is also facing these current challenges. Since 1963, the owner family Görtz – now with partner FSN – has been supplying delicious breads, rolls and cakes, as well as sweet and savoury snacks, to its regional customers, 362 days a year. The traditional company has always remained true to its recipe for success: “For our guests, we bake naturally, delicious and above all fresh every day.”
Taking the concept seriously, in 2024 the Görtz Bakery started tapping into new efficiency potential in existing production. Together with ADM Automation Technology GbR, the responsible parties went in search of new possibilities. The company from Warburg, eastern Westphalia, founded in 2022 and specializing in cutting-edge mechanical engineering and robotics systems for bakery products, took up the challenge in Ludwigshafen.
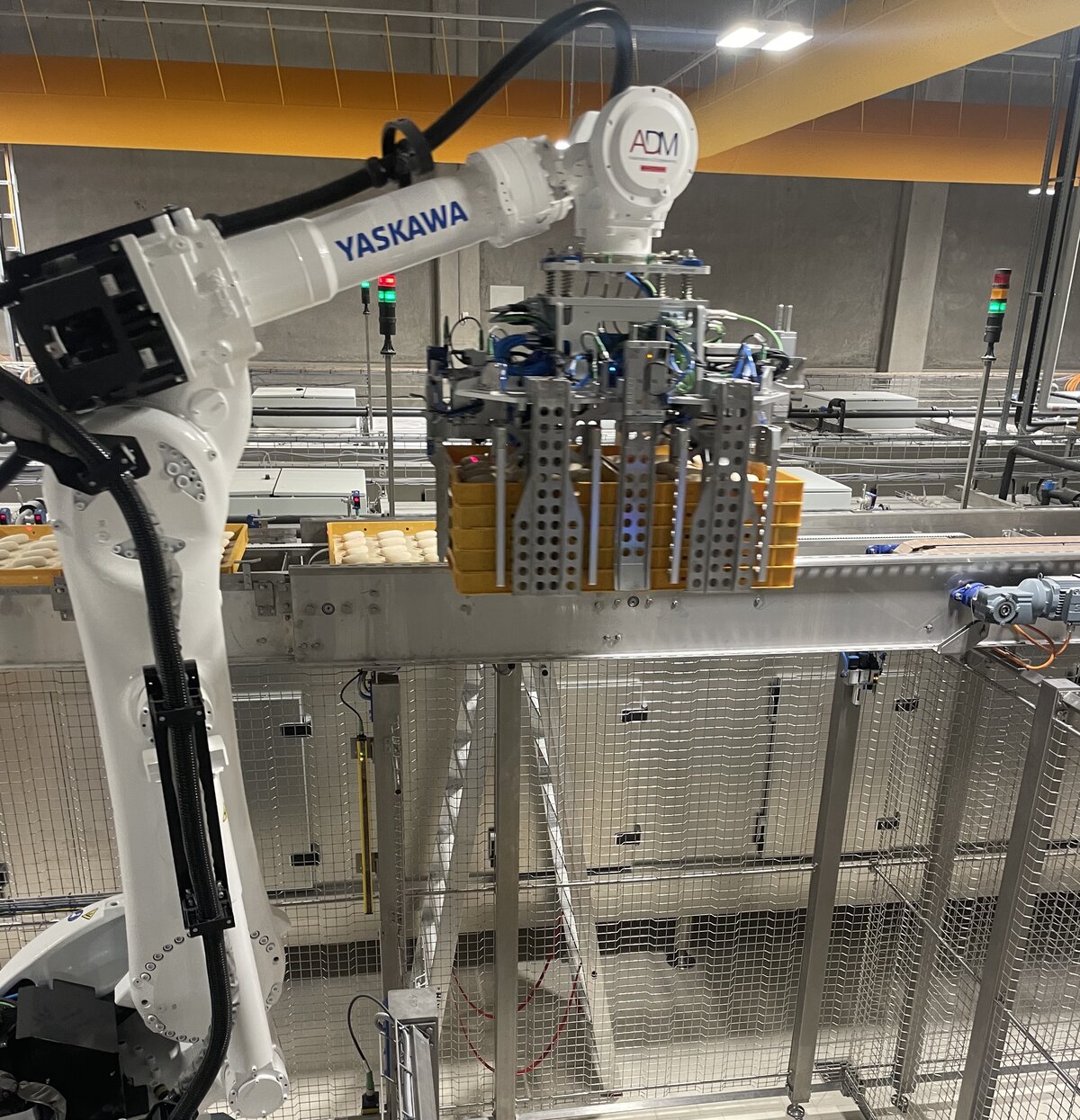
Picture: Automatic loading of trolleys is space-saving and secure.
Robotics meet complex requirements
The handling of dough pieces after freezing proved to be a promising starting point: the dough pieces each pass through one of two parallel freezing lines on baking sheets. These baking sheets must be automatically removed at the freezer outlet after freezing and transferred to trolleys.
The requirements for the project were clearly defined:
1. To ensure a consistently high product quality, the raw dough pieces on the baking sheets should not move during handling.
2. The limited spatial conditions should be taken into account.
3. The specified production capacity was high with 2000 baking sheets per hour (1000 baking sheets per freezer unit).
4. There should be no downtime when changing the trolleys, to ensure continuous and efficient production.
“After a thorough analysis, it quickly became clear that a purely mechanical solution would not provide the necessary compactness and flexibility to meet the special requirements of the Görtz bakery,” recalls ADM Managing Director Peter Dunschen. The decision was therefore made to introduce robotics. “This enabled a flexible and at the same time compact solution that perfectly satisfies both technical and spatial requirements.”
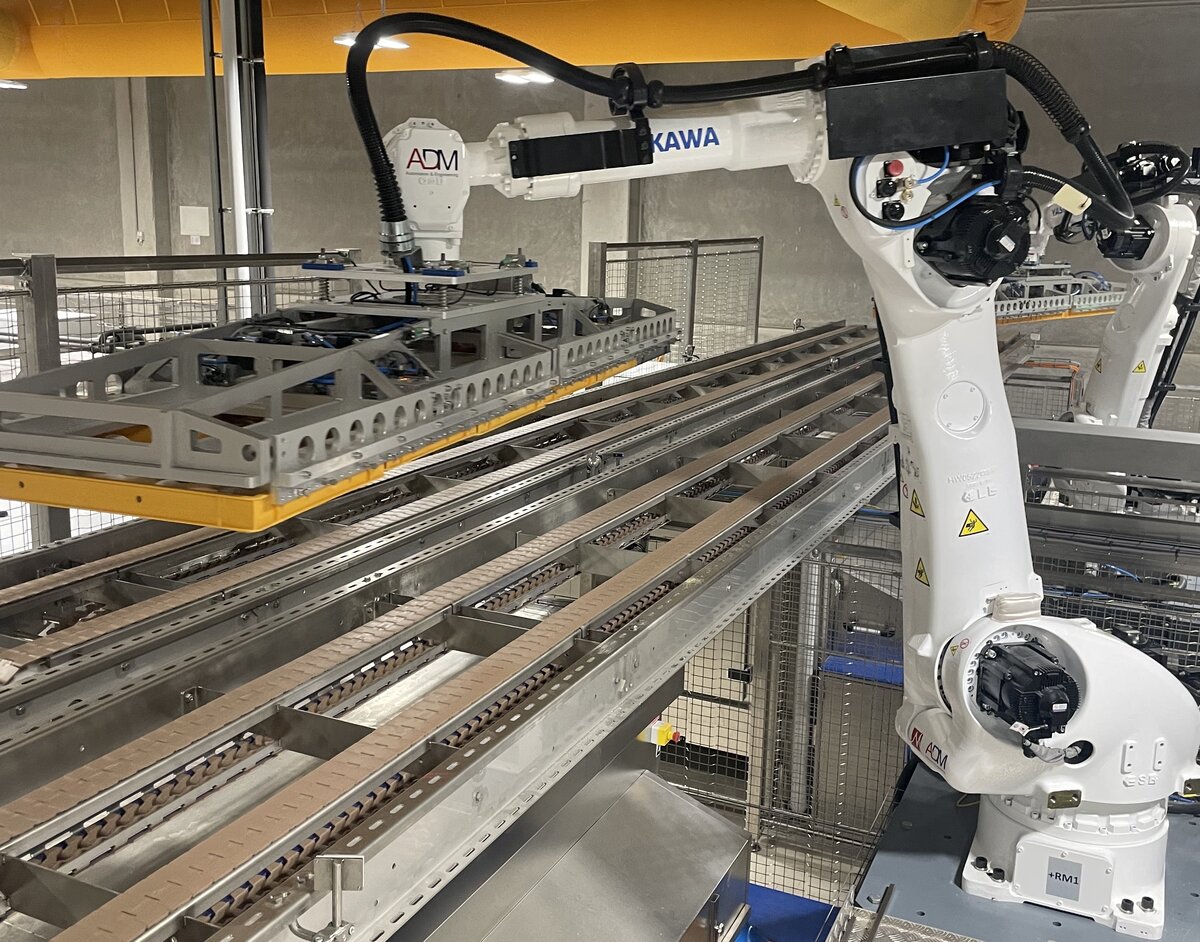
Picture: A specially developed ADM layer gripper allows the robot to simultaneously remove up to six baking sheets.
Robot-based system concept
The implemented system concept combines several innovative components in one system. A customized conveyor with a stopper separation was installed in the outlet area. This promotes proper layer formation of the baking sheets and ensures that the dough pieces are placed evenly and firmly on the baking sheets before they are removed by the robots.
As another key element, a total of four type MOTOMAN GP180 FGG industrial robots manufactured by Yaskawa will be used in the plant. The decision in their favour was based on the speed and precision on the one hand, load capacity of 180 kg and wide reach of the model on the other.
“GP” stands for “General Purpose” and thus a variety of applications. The 6-axis robots, manufactured at the European Yaskawa factory in Kočevje, Slovenia, can work in any installation position without restrictions. The robot cables can be inserted either sideways or through the base. The integrated media supply in the axles optimises the construction of grippers and ensures maximum reliability in later operation.
Yaskawa developed the robot series MOTOMAN GP FGG specifically for the food industry. FGG stands for “Food Grade Grease” and thus exclusive use of lubricants approved for food production. “This was a crucial factor for us, as we had to ensure the highest hygienic standards,” stresses ADM’s Dunschen. “Yaskawa’s GP180-FGG robot perfectly fulfils these requirements, ensuring even higher quality and safety of the entire system.”
Removing the baking sheets at the freezer outlet
A robot at the end of each line removes the baking sheets from the two parallel freezers. Each of the two robots can extract up to six baking sheets at the same time and place them on a conveyor belt using a specially developed ADM layer gripper. The conveyor belt transports the baking sheets to the next station: the trolley loader.
The robots work at finely-tuned speeds to ensure that the dough pieces do not move on the baking sheets during handling. This fine-tuning of the movement sequences is instrumental in preserving the quality of the dough pieces and ensuring a consistently high production quality.
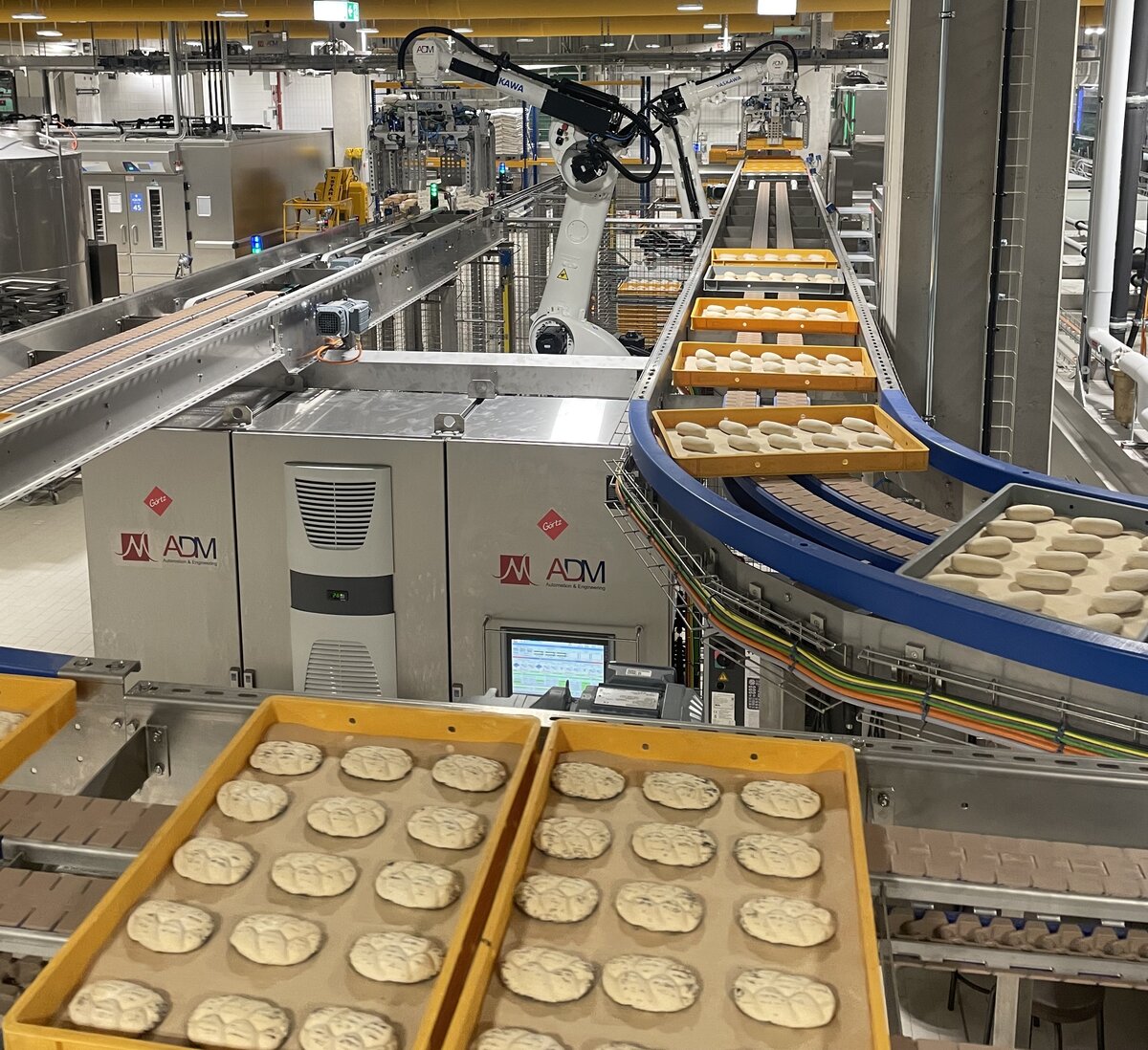
Picture: Two of the four Motoman GP180 robots remove the baking sheets from the freezer outlet and place them on a conveyor belt.
Loading the trolleys
Two other GP180 robots are responsible for precise stacking of the baking sheets on the trolley. These are equipped with a special layer gripper, which after picking up the stacks of sheets, also aligns them to ensure space-saving and stable loading of the trolleys. The gripper ensures that the baking sheets are loaded correctly on the trolley without displacement or instability. A safety light curtain provides the necessary security.
A particularly sophisticated feature of the solution allows the loading process of the trolleys to continue without interruption. As soon as one trolley is full, the robot automatically switches to a second cell, so that the loading process continues seamlessly. This ensures a continuous production flow and prevents downtimes that could detract from the efficiency of the plant. In the meantime, the operator has enough time to remove the full trolley and introduce a new empty trolley into the plant.
Successful premiere
The Görtz bakery has made an entry into the field of robotics with the new ADM system for automated handling of dough pieces. Besides optimizing its production process, the traditional Ludwigshafen-based company has achieved optimal use of the available space while ensuring high quality and efficiency.
The solution has been in successful operation since November 2024. “The end customer was very satisfied right from the beginning,” summarizes ADM Managing Director Peter Dunschen and adds: “After comprehensive training and the first practical application, it quickly became clear that the process is easy and intuitive to use. Despite initial concerns, everyone now gets along well with the robots.”
Source:
[1] WDR.de, 23.09.2024 (https://www1.wdr.de/nachrichten/westfalen-lippe/baeckereien-mehr-selbstbedienung-hoehere-umsaetze-100.html )
Author:
Stefan Westermann, Sales Manager, Yaskawa Europe GmbH, Robotics Division, DE-Allershausen
Contact for readers’ enquiries:
Tel. (+49) 8166-90-0
robotics@yaskawa.eu
Contact for the press:
Marion Annutsch
Marketing / PR / Communications
Yaskawa Europe GmbH
Tel.: +49-8166-90-0
marion.annutsch@yaskawa.eu
Photo source for all: ADM Automatisierungstechnik GbR